Corrosion of Stainless Steels and Zirconium Alloys in WWER-1000 Model Coolant with Addition of Zn and Al
Volodymyr Krasnorutskyy, Ivan Petelguzov, Viktor Grytsyna, Valeriy Zuyok, Mykhaylo Tretyakov, Roman Rud, Olena Slabospytska, Nadija Ishchenko, Natalia Svichkar
National Science Centre "Kharkiv Institute of Physics and Technology" ("Nuclear Fuel Cycle" Science and Technology Establishment), Kharkiv, Ukraine
Еmail address

(I. Petelguzov)
Citation
Volodymyr Krasnorutskyy, Ivan Petelguzov, Viktor Grytsyna, Valeriy Zuyok, Mykhaylo Tretyakov, Roman Rud, Olena Slabospytska, Nadija Ishchenko, Natalia Svichkar. Corrosion of Stainless Steels and Zirconium Alloys in WWER-1000 Model Coolant with Addition of Zn and Al. Journal of Materials Sciences and Applications. Vol. 2, No. 2, 2016, pp. 10-17.
Abstract
Long-term autoclave corrosion tests of stainless steel 08X18H10T and zirconium alloys E110 and Ukrainian pilot calciumthermal Zr1Nb (0.1% O) were carried out in the model coolant environment of WWER reactors with the addition of zinc or aluminum with aim to consider the possibility of using zinc or aluminum addition for improvement coolant on ukrainian WWER reactors. The corrosion kinetics and the condition of the oxide films were studied. It was shown that the addition of zinc improves the protective properties of the oxide films on stainless steels grade 08X18H10T and does not affect negatively on the corrosion resistance of zirconium alloys. The addition of aluminum appeared to be not sufficiently effective. The possible mechanism of the influence of zinc and aluminum on corrosion was considered.
Keywords
Stainless Steel, Zirconium Alloys, Corrosion, WWER Reactor, Model Coolant, Addition, Zinc, Aluminum
1. Introduction
One of the problems for the lifetime extension of NPPs is accumulating of radioactive corrosion products in the primary circuit. It complicates carrying out service activities. In world practice solutions for this issue are proposed and already applied the zinc injection into the primary coolant of PWR reactors. However the issue of reactor core and primary circuit materials corrosion of WWERs in Ukraine when injecting zinc has not been investigated yet before.
Since the commissioning of the first reactor units till now remains a pressing problem of creation and support of physical and chemical properties of the coolant, which would reduce the impact of unwanted corrosive effects. In order to solve this problem in Russia, Ukraine and a number of other countries held a large number of research works on coolant chemistry and investigation of corrosion processes in structural materials of WWERs [1].
Stable performance of Ukrainian WWER-1000 reactors is provided by applying ammonium-potassium slightly alkaline primary water chemistry [2]. One of the disadvantages of WWER primary water chemistry is the formation of large quantities of radioactive wastes due to high volumes of chemicals used. Another problem is the doserate buildup on the inner surfaces of primary circuit equipment during the long term operation of NPPs [3, 4].
Reduction of the amount of radioactive wastes and dose rate of equipment, according to the experience of PWR and BWR primary water chemistry optimization, can be achieved by the zinc injection into the primary coolant. Also there are other proposals to optimize primary water chemistry [5].
Research into the effects of corrosion of stainless steels and zirconium alloy influenced by zinc injection into the primary coolant of WWER core is presented in this paper.
One of the ways of reduction the amount of cobalt-60 in oxide deposits, instead of zinc injection, is to inject other elements with activation energy of the oxidation reaction greater, than that of cobalt.
It was proposed to inject aluminum instead of zinc [6].
In [7] showed that aluminum injection results in to have a higher protective properties and better adhesion to metal surface of oxide films on stainless steels.
Basing on these data, it was decided to research directly the effect of aluminum injection on the corrosion processes and the quality of the oxide films on stainless steels and zirconium alloys in an aqueous medium with the composition and parameters of WWER primary coolant.
2. Autoclave Conditions, Materials, Specimen Preparation
Autoclave tests of reactor primary circuit materials in conditions of WWER primary water were carried out in our research. The difference is that tests are carried out without reactor radiation and high-speed flow of coolant. In many cases, results of these tests agree closely with reactor tests as radiation damage for thermal reactors can not influence significantly the corrosion and diffusion processes on fuel rod claddings and other structural materials.
Specimens of 08X18H10T steel (GOST 5632-72), zirconium alloys Е110 (Zr+1% Nb) and developed in Ukraine experimental Zr1Nb (0.1% O) based on calciumthermic zirconium were prepared. Specimens were ground and etched (zirconium alloy) or electropolished (stainless steel). Each corrosion kinetics curve accounted for not less than 3 specimens. Data were averaged, the range within 10% of the mean value.
Model coolant substance is:
• 3,1 g/dm3 H3BO3;
• 0,025 g/dm3 KOH;
• 0,0056 g/dm3 NH3;
• H2O rest.
Addition of zinc in the solution is carried out from the zinc acetate (CHCOO)2Zn • 2H2O in calculating on 0.01 and 0.03 mg/dm3 zinc relative to 1 dm3 of water, analogicaly the addition of aluminum was produced from aluminum nitrate Al (NO3)3 • 9H2O in recalculation on the amount of 0.01 and 0.03 mg Al / dm3 of water model coolant.
3. Corrosion of Stainless Steel and Zr Alloys in WWER Model Coolant with Zinc at 350, 325, 300°С
3.1. Corrosion at 350°С
Corrosion tests of 08X18H10T steel and zirconium alloys Е110 and Zr1Nb (0.1% О) specimens were carried out in the WWER-1000 model coolant environment at 350°C and 16.5 MPa.
The results of kinetic evaluations during testing specimens are presented on Fig. 1-9. Corrosion kinetics of steel 08X18H10T at 350°C is characterized by mass gain, but in the medium with 0.01 mg/dm3 zinc mass gain is slower (Fig. 1). At the beginning of corrosion tests in the medium without zinc it was observer the mass gain and further mass loss.
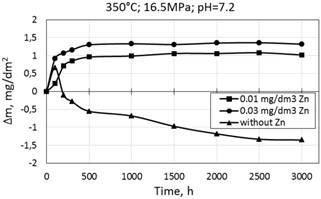
Figure 1. Corrosion kinetics of 08Х18Н10Т stainless steel in WWER model coolant at 350°С and 16.5 МPа with 0.01 and 0.03 mg/dm3 Zn and without Zn.
According to our previous research results [6] the reason of the mass loss is partial dissolution of outer layer of oxide films on stainless steels in the WWER primary coolant water in operating conditions. It was revealed that there is some difference in density and uniformity of oxide films on stainless steels after oxidation.
Table 1. Coefficients in corrosion equation of zirconium alloys ∆m/S = ktn and mass gain during 1500 hours for oxidation at temperature 350°С.
t, °C | Alloy | Corrosion environment | k | n | ∆m during 1500 h, mg/dm2 |
350 | Zr1Nb (0.1%O) | pH=7.2; 0.01mg/dm3 Zn | 1.48 | 0.36 | 21 |
Е110 | 1.69 | 0.35 | 22 |
Zr1Nb (0.1%O) | pH=7.2; 0.03mg/dm3 Zn | 1.40 | 0.36 | 20 |
Е110 | 1.76 | 0.34 | 22.5 |
Zr1Nb (0.1%O) | WWER primary water | 2.16 | 0.31 | 22.5 |
Е110 | 2.55 | 0.29 | 25 |
Corrosion kinetics of zirconium alloys significantly differs from stainless steels. On stainless steels the outer layer of oxide film dissolves and oxide film on zirconium alloy is strong, solid and insoluble in autoclave conditions (in reactor core conditions slight dissolution of the ZrO2 film is possible).
Corrosion kinetics of zirconium alloys is characterized by mass gain described by the cubic-type equation Δm/S=kt0.3 (Fig. 2, Table 1).
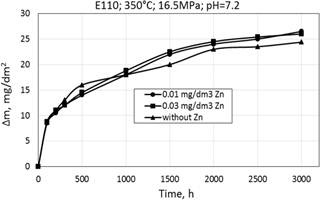
а
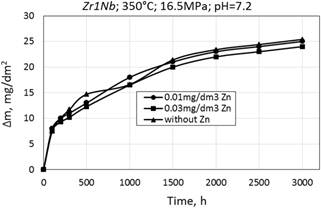
b
Figure 2. Corrosion kinetics of zirconium alloys Е110 (а) and Zr1Nb (0.1%O) (b) in WWER-1000 model coolant with 0.01 mg/dm3 Zn, 0.03 mg/dm3 Zn and without Zn.
Corrosion kinetics for alloys E110 and calciumthermic Zr1Nb (0.1%O) are almost similar when oxidized in WWER primary water with and without zinc, but there is a slight increase of the mass gain for calciumthermic Zr1Nb (0.1% O) (Fig. 2, Table 1).
Mass gain for all cases are in the range of 20-25 mg/dm2. A small difference in mass gain is expected to investigate more thoroughly in future research on this topic.
3.2. Corrosion at 325°С
The results of corrosion tests of stainless steel 08X18H10T and zirconium alloys in WWER-1000 primary water at 325°C and 12.5 MPa are shown in Fig. 3.
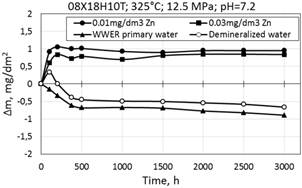
Figure 3. Corrosion kinetics of steel 08Х18Н10Т in WWER-1000 model coolant with 0.01 mg/dm3 Zn; 0.03 mg/dm3 Zn and in demineralized water at 325°С and 12.5 МPа.
As can be seen (Fig. 3), the corrosion kinetics of steel 08X18H10T specimens at 325°C is similar to the corrosion kinetics at 350°C of – there is also mass gain at the beginning of tests and subsequent slowing of mass changing. At the beginning of corrosion tests in WWER primary water without zinc it was observed a short time mass gain, and then goes gradual mass loss (Fig. 2).
It should be noted that there was a slight mass change of specimens, which indicates a very low corrosion rate in both environments with and without zinc and high general corrosion resistance of stainless steel.
Also in Fig. 3 are shown graphs of mass change for 08X18H10T specimens tested in WWER primary water and demineralized water for steel that characterize the mass loss with time.
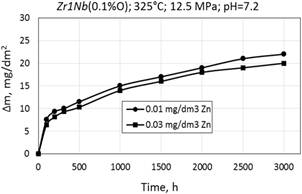
Figure 4. Corrosion kinetics of zirconium alloy Zr1Nb (0.01%O) in WWER-1000 model coolant with 0.01 mg/dm3 Zn and 0.03 mg/dm3 Zn at 325°С and 12.5 МPа.
Corrosion kinetics of zirconium alloys in WWER primary water with 0.01 dm3 and 0.03 dm3 Zn was different (Fig. 4). This suggests that there is no adverse effect of zinc addition on the corrosion resistance of fuel rod cladding material made of zirconium alloy.
3.3. Corrosion at 300°С
The results of corrosion tests of 08X18H10T steel and zirconium alloys E110 and Zr1Nb (0.1% O) in WWER-1000 model water coolant at 300°C and 8.6 MPa are shown in Fig. 5 and 6.
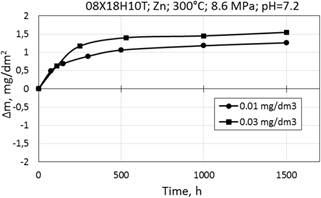
Figure 5. Corrosion kinetics of steel 08Х18Н10Т in WWER-1000 model coolant with 0.01 mg/dm3 Zn (a); 0.03 mg/dm3 Zn (b) at 300°С.
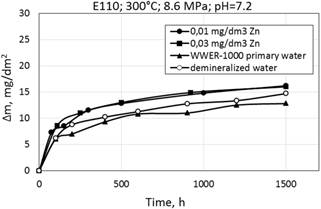
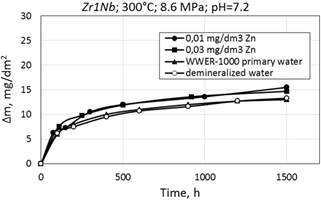
Figure 6. Corrosion kinetics of zirconium alloys E110 (a) and Zr1Nb (0.1%O) (b) in WWER-1000 model coolant with 0.01 mg/dm3 Zn; 0.03 mg/dm3 Zn; without Zn and demineralized water at 300°С and 8.6 MPa.
Corrosion kinetics of zirconium alloys in WWER primary water and in demineralized water is shown in Fig. 6. It was observed the decrease of mass gain after testing in these environments. To clarify the characteristics of corrosion kinetics of different materials it is desired to carry out long-term tests.
Oxidation of zirconium alloys at 300°C in water environments is characterized by parabolic or cubic-type equation. Formed oxide films are stable and protective.
There are little differences in mass gain (or thickness of oxide films), depending on the composition of alloy or zinc concentration in water during the period of testing.
As can be seen, the mass gain in WWER primary water with Zn, showed a slight decrease in values during testing at 300°C.
4. Corrosion of Stainless Steel and Zr Alloys in WWER Primary Coolant with Aluminum at 350, 325, 300°С
4.1. Corrosion at 350°С
Aluminum ions were introduced to the WWER-1000 primary coolant water as composition Al(NO3)3∙9H2O. The initial stage of oxidation of 08X18H10T steel is characterized by mass loss, further a certain stabilization and slight mass gain. (Fig. 7).
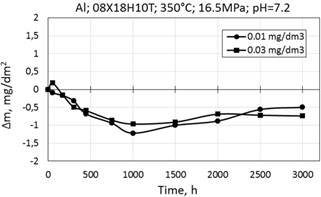
Figure 7. Corrosion kinetiсs of 08X18H10T stainless in WWER-1000 model coolant with 0.01 and 0.03 mg/dm3 Al at 350°C and 16.5 MPa.
The difference in the corrosion kinetics of 08X18H10T steel in media with 0.01 and 0.03 mg/dm3 of Al is insignificant, and samples have similar appearance.
Corrosion kinetics of zirconium alloys E110 and Ukrainian Zr1Nb (0.1% O) is similar when tested in media with and without aluminum (Fig. 8). Slight difference in mass gain is attributed to the experimental scatter measurements (Table. 2).
Table 2. Coefficients in corrosion equation of zirconium alloys ∆m/S = ktn and mass gain during 1500 h at 350°С.
Alloys | Corrosion media | k | n | ∆m during 3000 h, mg/dm2 |
Zr1Nb (0.1% O) | 0.01 mg/dm3 Al | 1.88 | 0.34 | 28.5 |
Е110 | 2.24 | 0.32 | 27.5 |
Zr1Nb (0.1% O) | 0.03 mg/dm3 Al | 4.13 | 0.23 | 27.0 |
Е110 | 4.18 | 0.25 | 29.0 |
Zr1Nb (0.1% O) | WWER primary water | 2.16 | 0.31 | 26.0 |
Е110 | 2.55 | 0.29 | 26.6 |
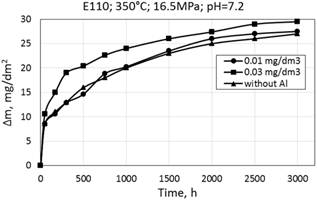
a
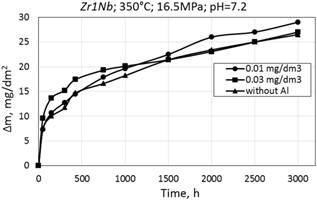
b
Figure 8. Corrosion kinetics of zirconium alloys E110 (a) and Zr1Nb (0.1% O) (b) in WWER-1000 model coolant with 0.01 and 0.03 mg/dm3 Al and without Al at 350°C and 16.5 MPa.
Mass gain data for all cases is in the range from 20 to 30 mg/dm2 for 3000 hours and the corrosion law is likely cubic.
4.2. Corrosion at 325°C
Corrosion kinetics of 08X18H10T steel at 325°C in WWER primary coolant with Al is generally similar to the corrosion kinetics at 350°C, except that at the initial stage of oxidation mass gain was observed, and further there was the mass loss (Fig. 9).
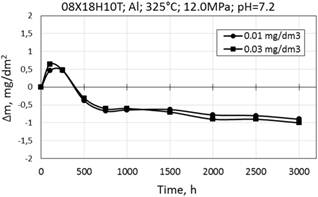
Figure 9. Corrosion kinetics of 08X18H10T in WWER-1000 model coolant with 0.01 and 0.03 mg/dm3 Al at 325°C and 12.0 MPa.
Corrosion kinetics of zirconium alloy Zr1Nb (0.1% O) in WWER primary water with different Al content is also similar. Data for comparison is presented in Fig. 10 and Table. 3.
Table 3. Coefficients in corrosion equation of zirconium alloys Δm/S = ktn and mass gain during 750 hours for oxidation at temperature 325°C.
Alloys | Concentration of Al | k | n | ∆m during 750 h, mg/dm2 |
Zr1Nb (0.1% O) | 0.01mg/dm3Al | 2.13 | 0.29 | 15.2 |
Zr1Nb (0.1% O) | 0.03mg/dm3Al | 2.175 | 0.31 | 16.1 |
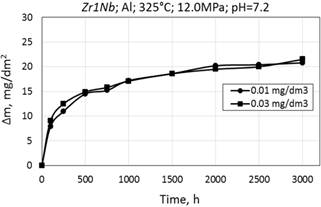
Figure 10. Corrosion kinetics of zirconium alloys E110 (a) and Zr1Nb (0.1% O) (b) alloy in WWER-1000 model coolant with 0.01 and 0.03 mg/dm3 Al at 325°C and 12.0 Mpa.
The oxidation of zirconium alloy Zr1Nb (0.1% O) in WWER primary coolant with 0.01 mg/dm3 and 0.03 mg/dm3 of aluminum at 325°C also corresponds to the cubic law. A slight mass gain was noticed for samples oxidized in medium with 0.03 mg/dm3 of aluminum.
4.3. Corrosion at 300°С
Corrosion kinetics of 08X18H10T steel in WWER primary water at 300°С and 8.6 MPa showed mass gain during the first half of testing period, further there was mass loss especially for concentration of 0.03 mg/dm3 of aluminum (Fig. 11).
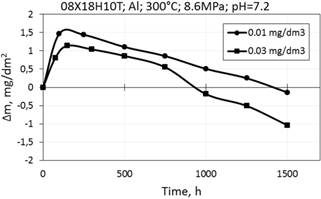
Figure 11. Corrosion kinetics of 08X18H10T steel in WWER-1000 model coolant with 0.01 mg/dm3 and 0.03 mg/dm3 Al at 300°C and 8.6 MPa.
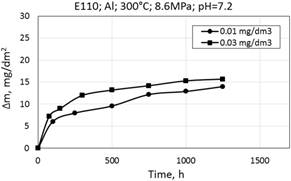
a
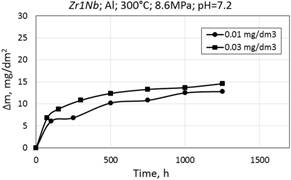
b
Figure 12. Corrosion kinetics of zirconium alloys E110 (a) and Zr1Nb (0.1%O) (b) in WWER-1000 model coolant with 0.01 mg/dm3 and 0.03 mg/dm3 Al at 300°C and 8.6 MPa.
Corrosion kinetics of zirconium alloys in WWER primary water at 300°С and 8.6 MPa with aluminum additive also corresponds to the cubic law (Fig. 12).
5. Oxide Films on Specimens After Oxidation
5.1. Appearance of Samples
The typical appearance of samples is shown in Fig. 13.
Oxide films on stainless steel samples after corrosion tests are uniform, loose, light brown and lackluster. Oxide films on zirconium alloys are uniform, adherent, dark gray and lustrous.
Surface of 08X18H10T steel specimens after testing in WWER primary water with and without Zn or Al have a similar appearance. Also, surface of zirconium alloys E110 and Zr1Nb (0.1%O) after oxidation are similar and no influence of zinc or aluminum was observed.
5.2. SEM Micrographs of Oxide Films on Stainless Steel
SEM micrographs of oxide film surface on stainless steel 08X18H10T formed in WWER primary water at 350°C and 16.5 MPa, are presented in Fig. 15. It is evident that during the testing outer layer of oxide film gradually changes towards loosening and partial dissolution or transformation.
Surface of oxide films on stainless steel after 250-750 hours of corrosion tests in WWER primary water with Zn appeared to be more uniform and continuous, but also there were some small defects (Fig. 16a, b). After 1500 h of testing the dissolution or transformation of the outer oxide layer was observed (Fig. 15c, d).
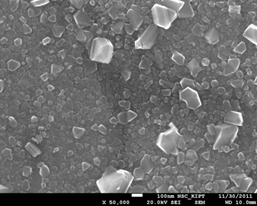
Figure 15. SEM micrograph of oxide film surface on 08Х18Н10Т steel after corrosion tests in WWER-1000 model coolant with 0.03 mg/dm3 Zn, at 350°С; after 1500 h.
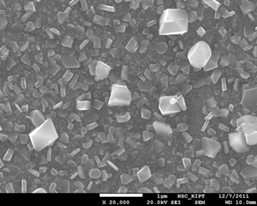
Figure 16. View of oxidized steel surface 08X18H10T sample after testing in PWR model coolant medium supplemented with 0.03 mg / dm3 in Al for 2000 hours at 350°C.
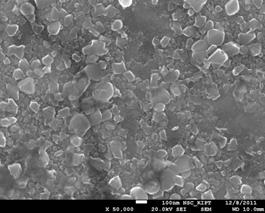
Figure 17. View of oxidized steel surface 08X18H10T sample after testing in a simulated PWR coolant medium whithout supplement the ingibitors for 2000 hours for 350°C (x50000).
As can be seen, oxide film is uniform with a small amount of white precipitates. On the oxide film surface there are scarce pits and pores with the size 5 - 10 microns. These white precipitates have a crystalline structure and size 1-3 microns. Basing on the literature data and the SEM data we suppose that these white precipitates are crystals of magnetite (Fe3O4) or hematite (Fe2O3) [8].
6. Discussion
Autoclave corrosion tests in WWER primary water at different temperatures revealed complex and irregular character of corrosion processes on stainless steel, i.e. mass gain at the beginning of tests and further gradual mass loss depending on the testing duration, temperature and pH. As shown in our previous work [9], the phenomenon of mass loss on stainless steel specimens is explained by partial dissolution of the outer layer of oxide film. Corrosion kinetics of stainless steel in demineralized water also characterized by mass loss.
Carried out tests revealed that oxide films on stainless steels become more compact when zinc added into corrosion media. Formation of oxide films in WWER-1000 primary water with zinc is characterized by mass gain, but not loss.
In general, the protective properties of oxide films on stainless steels are high, as evidenced by slowing of mass loss over time, albeit with varying rates. This mass loss is negligible. As shown in SEM micrographs there is partial dissolution of the outer layer of oxide films, occurrence of small amount of corrosion pits and formation of crystals on the surface.
It should be mentioned that in the temperature range of 300... 350°C difference in the value of mass changes of 08X18H10T specimens is negligible. This suggests that corrosion mechanisms and properties of oxide films are also similar in this temperature range.
Influence of zinc on formation of oxide films on stainless steels in high-temperature water environments is the following: Zn is able to replace Co, Fe, Cr, Mn in the spinel layer. It is caused by the fact that for example, zinc ferrite (ZnFe2O4 franklinite) possess a higher free energy of formation of (303 kcal/mol) than that of magnetite (290 kcal/mol) and ferrite (283 kcal/mol) and at the operating temperature of primary coolant causes a displacement of cobalt and some other elements by zinc [10]. These effects can lead to a decrease of corrosion rate of stainless steels, the detention of cobalt diffusion through the oxide film, reducing its release into the primary coolant, thus reducing the doserate in the primary circuit.
Oxide films on stainless steels consist of (CrFe)2O3 or its mixture with α-Fe2O3 after 24 hour tests. Longer tests lead to the formation of chromite spinel, which consists mainly of NiO(CrFe)2O3 [8, 11]. In our research we did not investigate the composition of oxide films but it could be of significant interest.
Corrosion kinetics of zirconium alloys E110 and Zr1Nb (0.1% O) in WWER-1000 primary water with zinc is similar to oxidation in water without zinc and in demineralized water. But there were some differences related to test conditions. No deterioration of the corrosion resistance of zirconium alloys under WWER-1000 primary coolant conditions with the addition of 0.01 or 0.03 mg/dm3 Zn was observed.
Instead of zinc, aluminum addition into primary coolant also is considered to apply. Introduction of aluminum ions into the oxide film facilitates due to its increased activation energy of oxidation. The advantage of aluminum in comparison with zinc is that it has no active isotopes [6, 7].
Carried out experiments with the addition of aluminum have not demonstrated its effectiveness at temperatures of 350 and 325°C. But at 300°C it was a slight tendency to improve the protective properties of oxide films on stainless steel (mass gain instead of mass loss) at the beginning of tests. Addition of aluminum to the WWER primary water showed no significant influence on corrosion resistance of zirconium alloys.
Experimental results revealed that the Zn and Al addition to the WWER-1000 primary water does not cause any adverse effects on the oxidation of zirconium alloys.
7. Conclusions
Corrosion processes on WWER-1000 primary circuit structural materials (stainless steel 08X18H10T and zirconium alloys E110 and experimental calciumthermal Zr1Nb) in primary water with Zn or Al were studied.
(1) Complex character of corrosion processes on stainless steels in primary coolant conditions was shown. Corrosion of stainless steels is accompanied by mass gain or loss often without regular function of time because oxide films are flocculent and the outer layer is soluble.
(2) Zinc addition to the water corrosion environment leads to the strengthening of oxide films on stainless steels, as evidenced by the tendency to mass gain instead of loss.
(3) The difference in corrosion rate of steel 08X18H10T in temperatures interval 300... 350°C is negligible, indicating a weak dependence of corrosion process on temperature in this interval. It is assumed that it is due to the fact that mass gain during the oxidation to some extent compensates by the rate of dissolution of the outer layer of oxide film.
(4) Zinc addition to the corrosion environment reduced the number of defects such as pits on the surface of oxide film, lead to its strengthening and formation of robust and uniform oxide films.
(5) There was no negative influence of zinc addition on the corrosion resistance of zirconium alloys in WWER-1000 primary water.
(6) Zinc addition to the WWER primary coolant leads to the increase of corrosion resistance of stainless steels, consequently the doserate is reduced allowing to increase safety and extend the lifetime of nuclear power plants.
(7) Aluminum addition did not cause any significant influence on corrosion resistance of stainless steels and zirconium alloys during short-term tests, but long-term studies may be carried out.
References
- V. F. Tyapkov, R. B. Sharafutdinov. Condition, main problem directions of improvement of water-chemical mode of AES. //Vestnik Gosatomnadzora Rossii, № 4, 2003 (in Russian).
- I. M. Fоltov, А. V. Аrkhipenko, А. N. Маskо. The influence of water chemistry on the safety, reliability and economy of NPP operation. //Sbornik dokladov Mezhdunarodnoi nauchno-tekhnicheskoi konferentsii МNТК-2008. Моskvа, 21-23 May 2008. (in Russian).
- I. M. Fоltov, А. V. Аrkhipenko, А. N. Маskо. The improvement of water-chemical regime of primary and secondary circuits of WWER NPP in Ukraine// Sbornik dokladov Mezhdunarodnoi nauchno-tekhnicheskoi konferentsii МNТК-2010. Моskvа, 2010. P. 77-87 (in Russian).
- J. Kysela. Activities of the Nuclear Research Institute in Water Coolant Interaction with Fuel and Primary Circuit Materials, Coolant Technology of Water Cooled Reactors, Vol 1. // Chemistry of Primary Coolant in Water Cooled Reactors, IAEA-TECDOC-667, IAEA, Vienna, 65, September 1992.
- V. A. Yurmanov, V. N. Belous, A. F. Chabak, I. V. Pirkov, Yu. P. Korchagin.Prospects of zinc injection into the coolant of domestic nuclear power plants // Sbornik dokladov Mezhdunarodnoi nauchno-tekhnicheskoi konferentsii МNТК-2008. Моskvа, 21-23 May 2008. (in Russian).
- T. V. Yepimakhov, A. A. Yefimof, O. Yu. Pykhteyev, L. N. Moskvin. Development of a methodology phases analizatory material joint products of the hydrolysis of Fe, Al and Co // Sbornik dokladov Mezhdunarodnoi nauchno-tekhnicheskoi konferentsii МNТК-2008. Моskvа, 21-23 May 2008. (in Russian).
- Yu. I. Slepokon, V. N. Kozhin, V. V. Prozorov, V. L. Doilnitsin, V. A. Yurmanov, V. N. Belous.Preparation of surfaces of process equipment when doing water chemistry with correctional treatment of the surface of the aluminum // Sbornik dokladov Mezhdunarodnoi nauchno-tekhnicheskoi konferentsii МNТК-2008. Моskvа, 21-23 May 2008. (in Russian).
- W. Kuang, X. Wu, E.-H. Han. The oxidation behaviour of 304 stainless steel in oxygenated high temperature water. // Corrosion Science, 2010, vol.52, pp. 4081–4087.
- V. S. Кrasnorutskyy, I. А. Petelguzov, V. М. Grytsyna, V. А. Zuyok, М. V. Тrеtyakov, R. А. Rud, N. V. Svichkar, Ye. А. Slabospytska, N. I. Ishchenko. Corrosion of stainless steels under the conditions simulating the primary coolant of WWER-1000. The corrosion behavior of the mixed fuel downloads//Voprosiatomnoinaukiitekhniki. 2011. №2.Seriya:Fizikaradiatsionnikh povrezhdeniiiradiatsionnoye materialovedeniye(97),p. 80-87(in Russian).
- I. Betova, M. Bojinov, P. Kinnunen, T. Saario. Zn injection in Pressurized Water Reactors laboratory tests, field experience and modeling. //Research Report, No VTT-R-05511-11 19.9,VTT Technical Research Centre of Finland, Espoo, 2011.
- J. S. Choi, S.-C. Park, K.-R. Park, H.-Y. Yang, O-B. Yang. Effect of zinc injection on the corrosion products in nuclear fuel assembly. //Natural Science Vol.5, No.2, 173-181 (2013).