The Effect of Speed on the Performance of a Two-Way Application of Cutting Fluid in Turning Process
S. O. Yakubu*, M. U. Bonet, D. K. Garba, J. A. Muhammed
Mechanical Engineering Department, Faculty of Engineering, Nigerian Defence Academy
Email address

(S. O. Yakubu)
*Corresponding author
Citation
S. O. Yakubu, M. U. Bonet, D. K. Garba, J. A. Muhammed. The Effect of Speed on the Performance of a Two-Way Application of Cutting Fluid in Turning Process. Engineering and Technology. Vol. 3, No. 6, 2016, pp. 106-109.
Abstract
The cutting speed is one the most important parameters of machining processes. It influences the tool life by influencing the tool wear rate, the surface quality of machined workpiece by influencing the surface roughness of the workpiece. The speed also affects the temperature at the cutting zone. Therefore, this research investigated the influence of speed on the effectiveness of the two-way application of cutting fluids (CF) in terms of the surface quality of the machined workpiece, tool wear and the temperature at the cutting zone. The research was conducted varying the angle of feeding from 30° to 180°, while the depth of cut and the feed rate were kept at constant values of 1.5 mm and 0.75mm/rev respectively. The speeds used were 63, 125 and 180 rpm respectively. The poorest performance of the cutting fluid (CF) was achieved when the speed was 125 rpm particularly in terms of the tool life and temperature, while the best performance of the CF was obtained under the speed value of 180 rpm particularly as regard the surface quality. The best surface quality (i.e. the lowest surface roughness) was 5.77µm when the angle of feeding was 150° followed 6.79µm at feeding angle of 60°. This certifies the fact that the angle of feeding affects the performance of the CF. The lowest tool wear value (the highest tool life) was established under the speed of 63 rpm corresponding to 0,04mm, while the lowest temperature was 24.54°C which was obtained at the speed of 180 rpm. The optimum speed recommended therefore, was 180 rpm.
Keywords
Cutting Fluid, Speed, Surface Roughness, Temperature, Cutting Fluid Feeding Angle
1. Introduction
Cutting process according to Yakubu S. O., etc [1,2,3], generates a lot of heat due to excessive temperature at the cutting zone. i.e. high temperature at the workpiece-cutting tool interface. This is due to the high friction and abrasion between these two faces as well as due to the high force required to shear the surface layer of the workpiece. The higher the force, the higher the intensity of the temperature at the cutting zone.
The excess cutting zone temperature will act negatively on the surface quality of the machined surface as well as its properties like the hardness, strength wear resistance etc. The dimensional accuracy of the machined surface can not be achieved with excessive cutting zone temperature [4]. The higher the temperature at the cutting zone, the faster the rate of the cutting tool wear. The tendency of the cutting tool becoming blunt is high at very high temperature due to the high rate of tool wear and formation of built up edge (BUE) [1,5]. This consequently causes poor surface finish and frequent replacement or re-sharpening of the cutting tool [1]
The aforementioned are some the reasons why cutting fluids/lubricants are applied to the cutting zone. But the method of its application affects its effectiveness/performance. This was establish in the works of Yakubu S. O. et al, [1,2], Diniz A. E & Micaroni R [6], Xavior M. A & Adithan M [7], Md Abdul Hasib et al [8] and ME Indian Institute of Technology Karagpur [9].
It was established that the two-way application of CF was better than the one-way by Yakubu S. O., Izelu C. O. [1]
As we all know, the major parameters/variables of cutting (turning) process in lathe machining are the cutting depth, speed and feed rate. There is no cutting process that can be carried out without these three parameters. Therefore, they are vital variables that affect any lathe machining process. The speed is one of the most vital variables in machining. The speed of machining directly influences the type of surface finish obtained, the tool life and the quantity of heat generated.
Thus, the establishment of its influence on the two-way application of CF can not be over emphasized. In the work of Yakubu S. O et al, [2,10] it was established that both the angle of CF feeding and the depth of cut affect the performance of the two-way application.
The essence of this research work was then to find out the effect of cutting speed on the two-way application of CF and possibly to establish the optimum value of the cutting speed for better performance of the two-way application.
2. Materials and Method
2.1. Materials and Equipment
The materials used as the workpiece for the experimental research were medium carbon steel, the soluble oil as the cutting fluid (CF) and the two-way CF application device. Cemented carbide tool inserts type T107 and grade YG8, were used as the cutting tool. The equipment used were: the Surface Roughness Tester model, the Insize Digital Vernier Caliper, The non-contact surface temperature measuring device and XL400 Universal Lathe Machine.
2.2. Experimental Procedure
The materials and equipment used were similar to the ones used in Yakubu S. O, Izelu C. O, Aku S. Y and Apochi M. J works [1,2,10]. The experiments were carried out on XL 400 universal lathe machine. The experimental set up is shown in Fig. 2.1. The machining was done using the following variables: the depth of cut was 1.5mm and feed rate of 0.75 mm/rev, the speed values used were 63, 125 and 180 rpm respectively; while the angle of CF feeding was varied from 30 to 180° and the nozzles were positioned at a distance of 30° from each other.
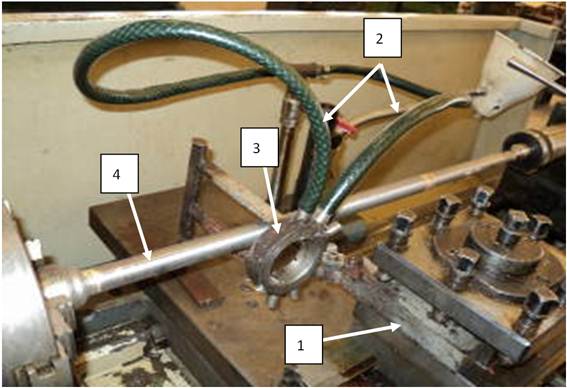
1 – Cutting Tool, 2 – Hoses, 3 – Two-way cutting feeding device, 4 - Workpiece
Fig. 2.1. Experimental Set Up.
The experiments were carried out on an interval of 20 minutes. The tool wear and the surface roughness of the machined surface values were measured after every 20 minutes, but the temperature values were measured using a German non contact temperature measuring instrument (Thermal Twin) during the cutting process. The surface roughness, the tool wear and the temperature values were measured at three different points and the average values were taken.
3. Results and Discussion
3.1. Results
Table 3.1. The effect of speed on the surface finish, tool wear and temperature at 30° feeding angle.
Speed, rpm | Angle of Feeding in Degrees = 30 |
Surface Roughness, µm | Tool Wear, mm | Temperature, °C |
63 | 12.04 | 0.11 | 26.77 |
125 | 11.08 | 0.43 | 31.83 |
180 | 8.87 | 0.13 | 27.12 |
Table 3.2. The effect of speed on the surface finish, tool wear and temperature at 60° feeding angle.
Speed, rpm | Angle of Feeding in Degrees = 60 |
Surface Roughness, µm | Tool Wear, mm | Temperature, °C |
63 | 10.23 | 0.07 | 29.32 |
125 | 11.25 | 0.38 | 31.63 |
180 | 6.79 | 0.11 | 24.54 |
Table 3.3. The effect of speed on the surface finish, tool wear and temperature at 90° feeding angle.
Speed, rpm | Angle of Feeding in Degrees = 90 |
Surface Roughness, µm | Tool Wear, mm | Temperature, °C |
63 | 11.18 | 0.11 | 29.58 |
125 | 11.29 | 0.41 | 31.48 |
180 | 8.35 | 0.11 | 27.75 |
Table 3.4. The effect of speed on the surface finish, tool wear and temperature at 120° feeding angle.
Speed, rpm | Angle of Feeding in Degrees = 120 |
Surface Roughness, µm | Tool Wear, mm | Temperature, °C |
63 | 8.83 | 0.06 | 28.70 |
125 | 11.96 | 0.39 | 31.30 |
180 | 10.76 | 0.19 | 30.50 |
Table 3.5. The effect of speed on the surface finish, tool wear and temperature at 150° feeding angle.
Speed, rpm | Angle of Feeding in Degrees = 150 |
Surface Roughness, µm | Tool Wear, mm | Temperature, °C |
63 | 11.08 | 0.05 | 28.83 |
125 | 10.68 | 0.34 | 24.90 |
180 | 5.77 | 0.13 | 25.60 |
Table 3.6. The effect of speed on the surface finish, tool wear and temperature at 180° feeding angle.
Speed, rpm | Angle of Feeding in Degrees = 180 |
Surface Roughness, µm | Tool Wear, mm | Temperature, °C |
63 | 10.28 | 0.04 | 28.03 |
125 | 10.25 | 0.44 | 31.83 |
180 | 8.75 | 0.11 | 29.85 |
3.2. Discussion
The influence of the speed on the two-way application of cutting fluid was established. It is worthy to note that the level of its influence on the two-way application of cutting fluid is further dictated by the feeding angle.
3.2.1. The Effect of Speed on the Surface Roughness (Surface Quality)
The surface roughness decreased from 12.04 µm to 8.87 µm as the speed was increased from 63 rpm to 180 rpm as evident in tables 3.1. In other words the surface roughness was decreased by about 26%. Generally, high values for surface roughness were obtained when the speed value was 125 rpm. This was also evident for other factors of machining determined, like tool wear and the cutting zone temperature.
The lowest surface roughness (5.77 µm) was obtained at the speed of 180 rpm and when the feeding angle was 150°. In other words, the best machined surface quality was achieved at the speed of 180 rpm with the feeding angle of 150° (Table 3.5)
The next best surface quality (6.79 µm) was established at the same speed of 180 rpm, but at feeding angle of 60° (Table 3.2). The next best surface quality was determined was when the surface roughness value was 8.35 µm (Table 3.3). In fact all surface roughness values obtained when the speed was 180° for all the feeding angles considered were lower than the values obtained when the speed values were 63 and 125 rpm respectively.
The surface roughness values under the speed of 63 and 125 rpm were relatively high as compared to the values obtained when the speed was 180 rpm.
3.2.2. The Effect of Speed on the Tool Wear
The lowest tool wear rate values were got when the speed was 63 rpm for any feeding angle as compared to the other two speed values that is, 125 and 180 rpm. The rate of tool wear increased drastically as the speed was increased from 63 to 125 rpm. But it dropped when the speed was further increased to 180 rpm.
Nonetheless, the values were higher than those obtained under the speed of 63 rpm. The sharp increase in the rate of the tool wear when the speed was 125 rpm might have been attributed to the rise in the temperature possibly due increase in the cutting force as a result of rise in the friction.
The lowest tool wear value was 0.04mm which was achieved under the speed of 63 rpm and at the feeding angle of 180°. Whereas, the highest value of tool wear (0.44 mm) was established at the speed value of 125 and at feeding angle of 180°.
At the speed of 180 rpm the tool wear rate was moderate. There was little or no difference between the values of the tool wear at any given feeding angle except when the feeding angle was 120°. In other words the values of the tool wear were between 0.11 mm and 0.13 mm. It was at the feeding of 120° that the value for tool wear was as high as 0.19 mm (see Table 3.4).
3.2.3. The Effect of Speed on the Temperature at the Cutting Zone
There was not between the values of the temperature for the three speeds used. The differences between the values were very small and same for the various feeding angles used.
At the speed of 63 rpm, the lowest temperature was 26.77°C and it was obtained at the feeding angle of 30° (Table 3.1) while the highest temperature was 29.58°C (table 3.3).
Higher values of temperatures were obtained when the speed was 125 rpm. This was reflected in the higher values of tool wear and surface roughness recorded at this speed. In fact the highest temperature (31.83°C) was gotten at this speed. These higher values were constant for the various angles of feeding except for angle 150° where a considerably low temperature was recorded corresponding to 24.90°C (see Table 3.5).
The temperature values were relatively moderate at the speed of 180 rpm. The highest temperature was 29.85°C and the lowest temperature was 24.54°C corresponding to feeding angles 180° and 60° respectively. In fact 24.54°C was the lowest temperature for all the speeds and feeding angles considered and this temperature was obtained at the feeding angle of 60°.
4. Conclusion and Recommendation
4.1. Conclusions
It is obvious that the speed has effect on any machining process. Therefore, lathe machining was not an exception. It was established that the speed actually influenced the performance of the turning process viz-a-viz the effectiveness of the two-way application of cutting fluid. That is, the effectiveness of the cutting fluid was influenced by the cutting speed.
The cutting fluid was more effective when the speed was 180 rpm in terms of the three factors determined viz-a-viz the surface roughness of the machined surface, the tool wear and temperature.
The lowest temperature and surface roughness (highest surface quality) was achieved under the speed of 180 rpm.
The values for tool wear, temperature and surface roughness for all the various angles used were relatively high when the speed was 125 rpm in comparison with the other two values of speed. i.e. 63 rpm and 128 rpm respectively. The high rate of tool wear and surface roughness was due to the rise in temperature which may be as a result of the increased friction at the workpice – cutting tool interface due to poor penetration of the CF to the cutting zone.
The most effective angles of CF feeding were 60° and 150°. A relatively low surface roughness and temperature was obtained under these angles when compared to other angles. The only exception was the rate of tool wear which was lower at the speed of 63 rpm compared to other two speeds for all the angles of CF feeding.
4.2. Recommendation
• it is recommended to machine the same material under the same conditions with the speed of 180 rpm for effective performance of the CF.
• Based on the obtained results, it is not recommended to machine the same material under the same conditions with the speed value of 125 rpm as the CF was least effect at this speed.
• The effective angles of CF feeding were 60° and 150°, while the most effective angle was 180°.
• More speed values can be used in future work to verify whether the optimum speed value of 180 rpm will be maintained.
• Material other than the medium carbon steel can be investigated in future to ascertain the effect of speed on the performance of the two-way application of CF.
Acknowledgement
I sincerely want to appreciate J. A. Muhammed and Ilyasu Suleiman for assisting me to conduct the experiments. My big thanks go to the Chief Technologist, A. I. Bokuta for availing the equipment used to carry out the research.
References
- S. O. Yakubu & C. O. Izelu (2013), "Design and Construction of a Cutting Fluid Two-way/Multi-Feeding Device for Turning Operation", British Journal of Applied Science and Technology (BJAST), Vol. 3 Issue No. 3, UK, Pp 598–608.
- Yakubu S. O., Aku S. Y., and Apochi M. J. (2014), "The Effect of Feeding Angle on the performance of a Two-Way Application of Cutting Fluids", Journal of Scientific Research and Reports (JSRR), Vol. 3, Issue 24, UK, Pp 3117–3125.
- R. K. Jain (2005), "Production Technology" 6th Edition, Khanna Publisher, India
- Serope Kalpakjian & Schmid Steve (2006), "Manufacturing Engineering Technology" Pp 623–626, publisher
- Colton J. S. (2009) "Machining, Chip formation, Cutting Fluids, Vibration and Chatter", Georgian Institute of Technology, USA, Pp 29-32.
- Deniz A. E. and Micaroni R (2007), "Influence of the direction of and flow rate of the cutting fluid on the tool life in turning process of AISI 1045 steel" International Journal of Machine Tools Manufacturing, USA, Pp 247–254.
- Xavior M. A. and Adithan M (2009), "Determining the Influence of CF on Tool Wear and the Surface Roughness during Turning of AISI 304 austenitic stainless Steel", Jounal of Material Process Technology, 209 (2), Pp 900–909.
- Md. Abdul Hasib, Abdullah Al-Faruk, Naseem Ahmed (2010), "Mist Application of Cutting Fluid", Int. Journal of Mechanical & Mechatronics Engineering (IJMME - IJENS)", vol. 10, No. 4.
- Indian Institute of Technology, "Control of Cutting Temperature and Cutting Fluid Application" Version 2 ME IIT, Kharagpur, accessed on 30th August, 2013. Available onwww.courseherocom/sitemap/schools/3264-indian. institute of technology Kharagpur/cou
- S. O. Yakubu & D. K. Garba (2016), "The influence of the depth of cut on the two-way application of cutting fluids", British Journal of Applied Science & Technology (BJAST), Vol. 12, issue 3, Pp 1-6, UK.