Inquisition the Purport of Weaving Conformation on Tearing Strength
Nasrin Ferdous, Reashad Bin Kabir
Department of Apparel Manufacturing Management & Technology, Shanto-Mariam University of Creative Technology, Dhaka, Bangladesh
Email address

(R. B. Kabir)
Citation
Nasrin Ferdous, Reashad Bin Kabir. Inquisition the Purport of Weaving Conformation on Tearing Strength. American Journal of Science and Technology. Vol. 3, No. 4, 2016, pp. 97-107.
Abstract
Fabric performance has immensely correlated with tearing strength; as throughout the test the yarns wreck one by one and that is the basic reason for fabric breakdown during usage. The endeavor of this effort is to study a number of factors affecting the tearing strength of different weave structure. Fundamentally ASTM D2261-07 Standard Test Method for Tearing Strength of Fabrics by the Tongue (Single Rip) Procedure (Constant-Rate-of Extension Tensile Testing Machine) was scrutinized in order to hit upon the precise outcome.
Keywords
Tearing Strength, Weaving Conformation, Textile, Tearing Strength Test
1. Introduction
The variety of fabric structures is divided into four groups as woven, knitted, braids and nonwovens [1]. Basic weave can be classified into three major types: i) Plain ii) Twill and iii) Satin/Sateen. There are other types of weaves are available like Matt weave, Diamond weave [2]. The useful life for clothing and other fabrics can be designated by Tearing strength [3]. In contrast with tensile strength, the magnitude of tearing strength spirals from the fact that it is further intimately allied to serviceability. Thus, an appraisal of fabric utility, perhaps it might play a great role [4]. Buyers add a demand of minimum fabric strength to the mandatory fabric specifications because it is not only an indication of fabric quality but also of yarn and fiber used in the fabric [5]. Assumption or Prediction of fabric mechanical properties such as strength, elongation, bending and shear is an intricate task, as it requires complete understanding of fabric structural mechanics and the interaction between warp and weft threads. Therefore, the solution of the fabric strength prediction problem could be performed by employing the empirical and computational models such as artificial neural network (ANN) or classical regression analysis [6]. However, The Tearing Strength is a measure of the resistance to tearing of either the warp or weft series of yarns in a woven fabric. A fabric which tears easily is regarded as an inferior product. The amount of resistance of a fabric to tearing is often important and particularly in fabrics like Bandage Cloth, Adhesive Tapes Military Fabric and so on [7]. The utility of a torn article is reduced; at best it is patched up and may be used for a less important job and at worst the article is scrapped. The resistance of a fabric to tearing has been studied by various laboratories and some general conclusion has been drawn:
i. Threads break singly or in very small groups during the tear therefore the single-thread strength of the component yarn is of great importance.
ii. High-set fabrics preclude thread movement and the assistance by thread grouping is therefore greatly reduced [8].
2. Literature Review
Tearing Strength of the fabric is mainly depends on fiber, yarn and fabric characteristics along with mechanical and chemical finishing treatments applied to the fabrics. Over the yarns, researchers has been directed to investigate the influence of yarn parameters (single yarn strength, uniformity, linear density, smoothness, extensibility, twist and type of yarn)and fabric parameters (weave, fabric sett, crimp and weight/m2) on Tearing Strength. A few studies related to the effect of fiber characteristics have also been reported. The majority of these investigations were executed through the utilization of yarns spun from ring spinning technology [9]. Compact spinning is a modified version of ring spinning process that is developed recently to produce yarns of better quality and smooth structure through better utilization of fiber properties [10-12]. Apart from this, the tearing strength is affected by changes in yarn geometry, fabric geometry, relaxation of the fibers and their frictional characteristics. The movement of the yarns will be restricted in tight constructions and results in a low tearing strength. Loose and open constructions allow yarns to move and group together, thus result in a high tearing strength. The tear strength is high with the designs having groups of yarnswoven together, such as rib weaves and basket weaves [13].
3. Materials & Methods
3.1. Materials
In order to perform this particular work, Rapier Loom used for manufacturing fabric. The manufactured fabric was Plain, Matt, Twill, Diamond and Sateen/Satin. Then samples were prepared for tearing strength test and tested by Titan Universal Strength Tester. For measuring GSM, GSM cutter and electric balance were used.
Fabric specification:
×64.5''
Temp. & R.H (%): 28°C, 65% R.H.
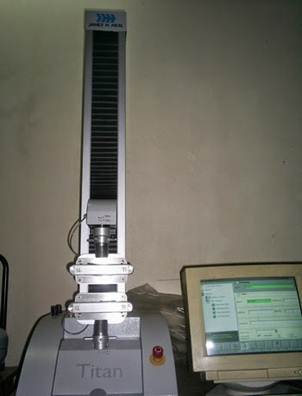
Fig. 1. Titan Universal Strength Tester.
3.2. Methods
The maximum force required to tear a specimen is called tearing strength. The force acting substantially parallel to the major axes of the test specimen.
ASTM D2261-07(Tearing Strength Test):
ASTM D2261-07 Standard Test Method for Tearing Strength of Fabrics by the Tongue (Single Rip) Procedure (Constant-Rate-of-Extension Tensile Testing Machine)
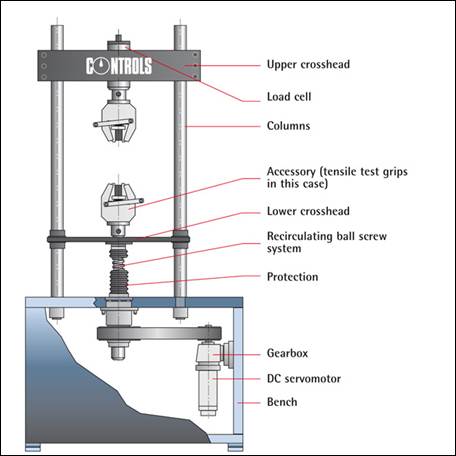
Fig. 2. Fabric Tensile Test device.
a) This test method covers the measurement of the tearing strength of textile fabrics by the tongue (single rip) procedure using a recording constant-rate-of-extension-type (CRE) tensile testing machine.
b) This test method applies to most fabrics including woven fabrics, air bag fabrics, blankets, napped fabrics, knit fabrics, layered fabrics, pile fabrics. The fabrics may be untreated, heavily sized, coated, resin-treated, or otherwise treated. Instructions are provided for testing specimens with or without wetting.
c) Tear strength, as measured in this test method, requires that the tear be initiated before testing. The reported value obtained is not directly related to the force required to initiate or start a tear.
d) Two calculations for tongue tearing strength are provided: the single-peak force and the average of five highest peak forces.
e) The values stated in either SI units or inch-pound units are to be regarded as the standard. The inch-pound units may be approximate.
Test Method Synopsis:
A rectangularspecimen, cut in the centre of a short edge to form a two-tongued (trouser shaped) specimen, in which one tongue of the specimen is gripped in the upper jaw and the other tongue is gripped in the lower jaw of a tensile testing machine. The separation of the jaws is continuously increased to apply a force to promulgate the tear. At the same time, the force developed is recorded. The force to continue the tear is calculated from autographic chart recorders or microprocessor data collection systems.
Connotation and Utilization:
a) This test method is considered satisfactory for acceptance testing of commercial shipments since current estimates of laboratory precision are acceptable, and the test method is used extensively in the trade for acceptance testing.
b) Depending on the nature of the specimen, the data recording devices will show the tearing force in the form of a peak or peaks. The highest peaks appear to reflect the strength of the yarn components, fiber bonds, or fiber interlocks, individually or in combination, needed to stop a tear in a fabric of the same construction.
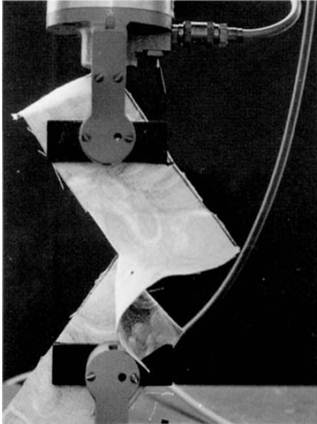
Fig. 3. Sample for Tearing Strength.
c) Most textile fabrics can be tested by this test method. Some modification of clamping techniques may be necessary for a given fabric due to its structure. Strong fabric or fabrics made from glass fibers usually require special adaptation to prevent them from slipping in the clamps or being damaged as a result of being gripped in the clamps.
d) The CRE-type is the preferred tearing testing machine. This test method allows the use of the CRT-type tensile machine when agreed upon between the purchaser and the supplier.
4. Experimental
4.1. Tearing Strength Test Procedure
i. For the tearing strength test ASTM D2261 method used. For doing this test at first a fabric specimen of 200 mm length and 75mm width taken. At the middle point of specimen width we cut 3 inch inner side and made a mark at more 75 mm inner side. Then placed the two end of the cut point into two jaws of the Titan tearing strength tester. Subsequently starting to test, and fabric was teared through the middle vertical line up to 75 mm. Then a graph found from computer software. After that we found mean tearing force was also foundfrom top five tearing points from the graph.
ii. Tearing Strength Test Specimen:
Test Method:ASTM D2261
Jaw Size:Upper Jaw= 100x25 mm
Lower Jaw= 100x25mm
Specimen Size:Length= 200mm
Width:75 mm
Pre-tension:2N
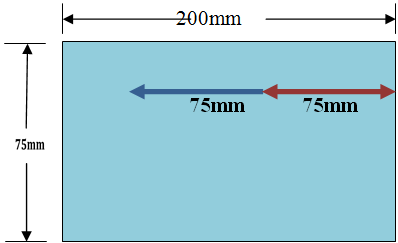
Fig. 4. Tearing strength test fabric specimen.
4.2. Graphical Representation for Each Weave
i. Plain Weave:
For Warp
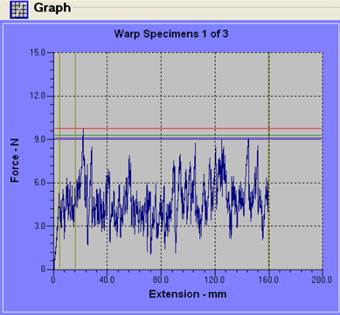
Fig. 5. (Specimen 1).
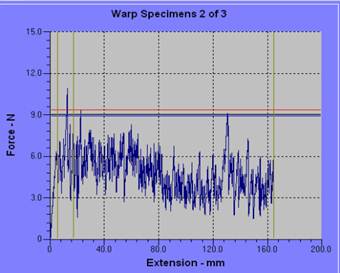
Fig. 6. (Specimen 2).

Fig. 7. (Specimen 3).
For Weft
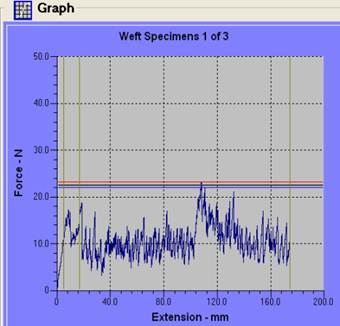
Fig. 8. (Specimen 1).
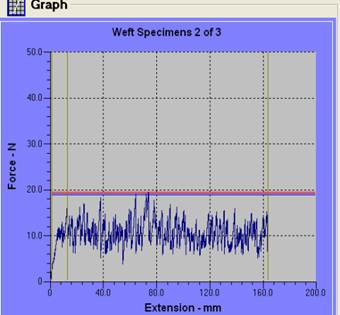
Fig. 9. (Specimen2).
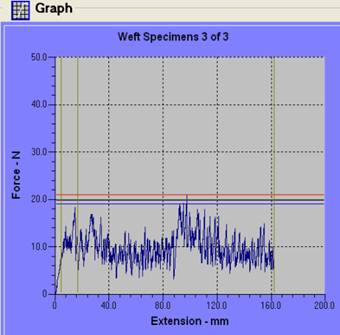
Fig. 10. (Specimen 3).
Table 1. Tearing strength test for plain weave fabric.
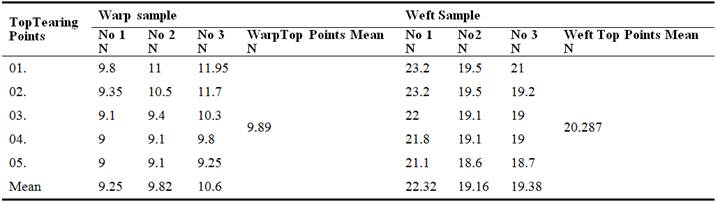
ii. Matt Weave
For Warp
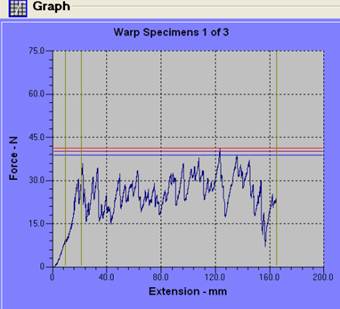
Fig. 11. (Specimen 1).
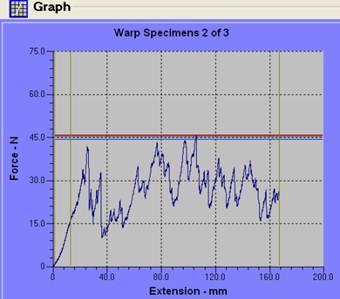
Fig. 12. (Specimen 2).
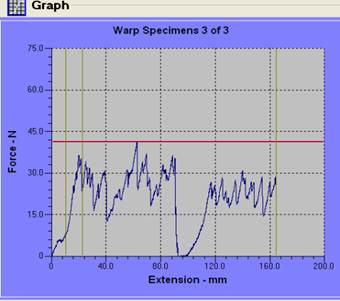
Fig. 13. (Specimen 3).
For Weft
Table 2. Tearing strength test for Matt weave fabric.
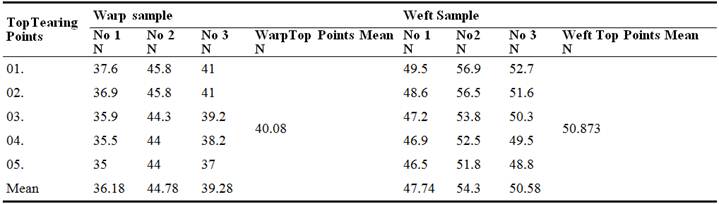
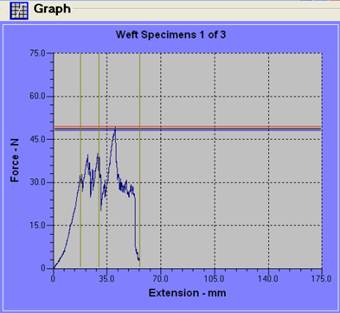
Fig. 14. (Specimen 1).
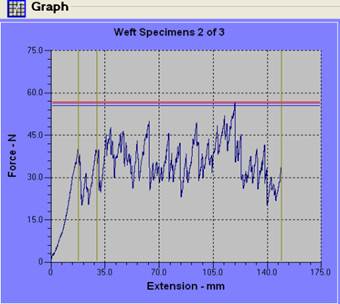
Fig. 15. (Specimen 2).
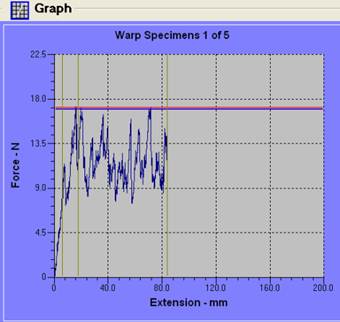
Fig. 16. (Specimen 3).
iii. Twill Weave:
ForWarp
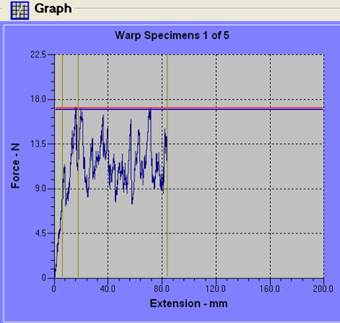
Fig. 17. (Specimen 1).
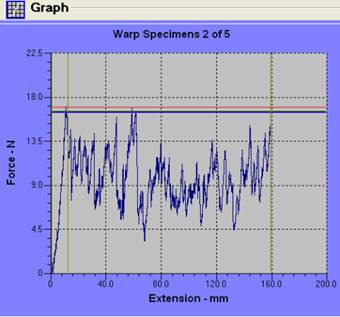
Fig. 18. (Specimen 2).
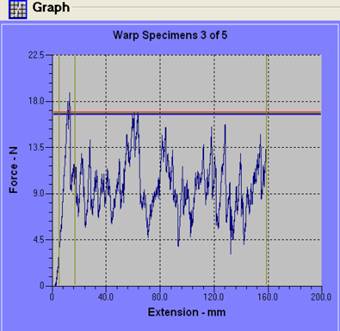
Fig. 19. (Specimen 3).
For Weft
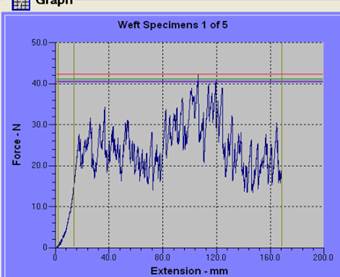
Fig. 20. (Specimen 1).
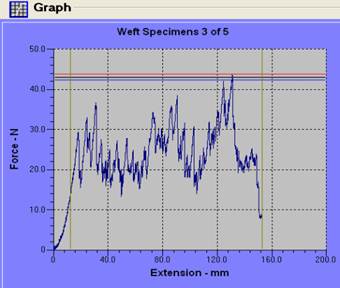
Fig. 21. (Specimen 2).
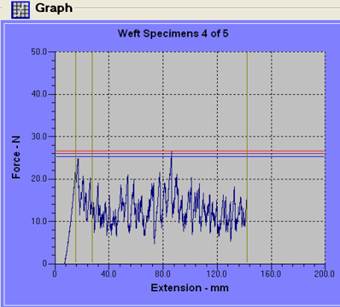
Fig. 22. (Specimen 3).
Table 3. Tearing strength test for Twill weave fabric.

iv. Diamond Weave:
For Warp
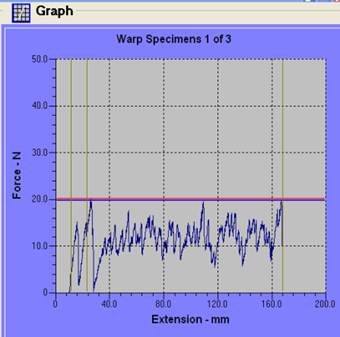
Fig. 23. (Specimen 1).
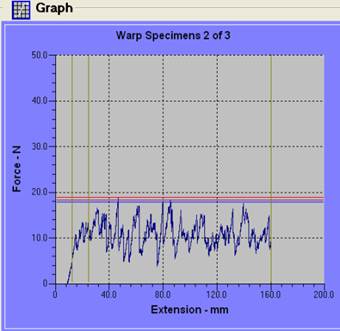
Fig. 24. (Specimen 2).
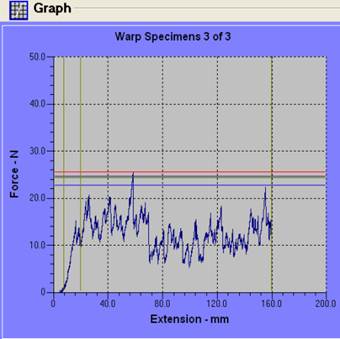
Fig. 25. (Specimen 3).
For Weft
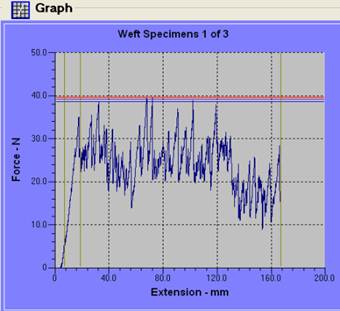
Fig. 26. (Specimen 1).
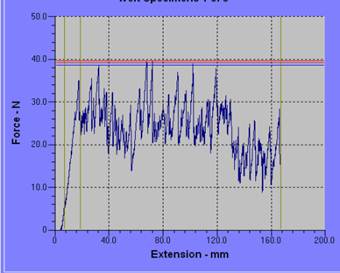
Fig. 27. (Specimen 2).
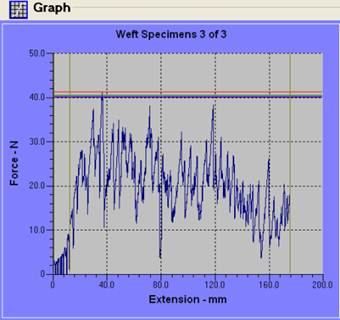
Fig. 28. (Specimen 3).
Table 4. Tearing strength test for Diamond weave fabric.
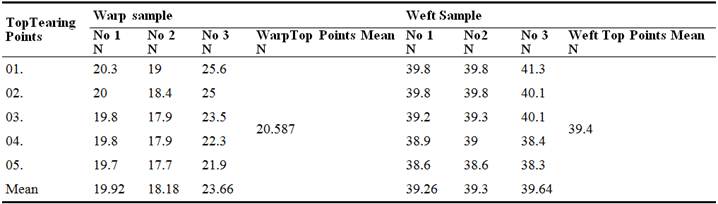
v. Sateen Weave:
For Warp
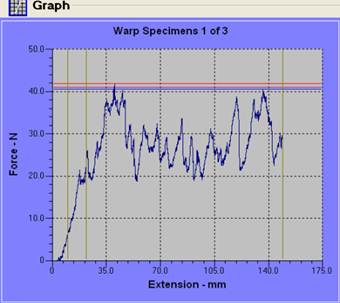
Fig. 29. (Specimen 1).
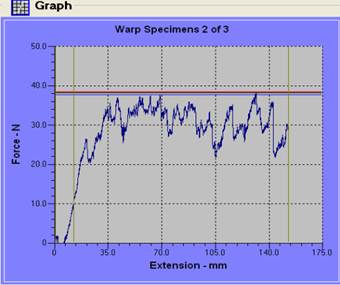
Fig. 30. (Specimen 2).
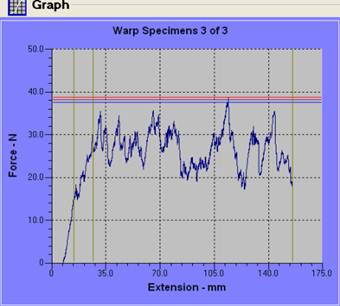
Fig. 31. (Specimen 3).
For Weft
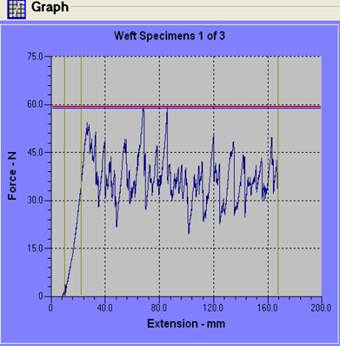
Fig. 32. (Specimen 1).
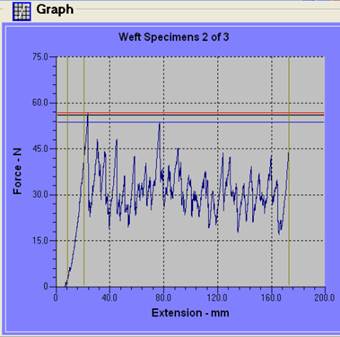
Fig. 33. (Specimen 2).
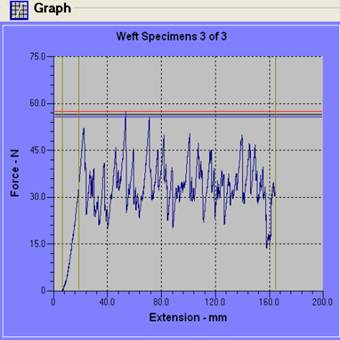
Fig. 34. (Specimen 3).
Table 5. Tearing strength test for Sateen Weave fabric.
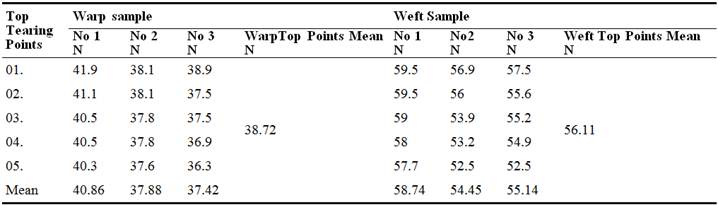
Table 6. Result for Tearing Strength Test at a glance.
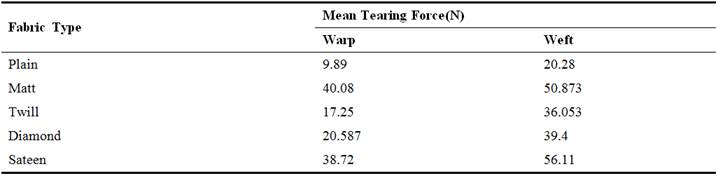
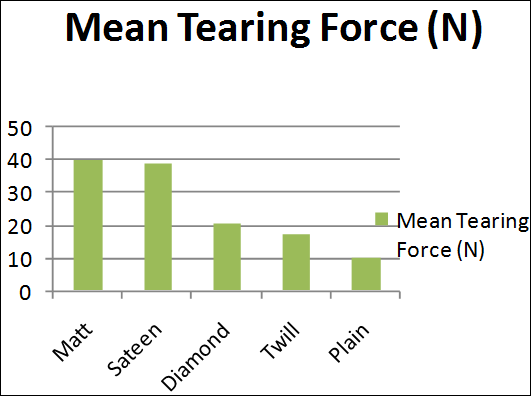
Fig. 35. Mean Tearing Force for Warp.
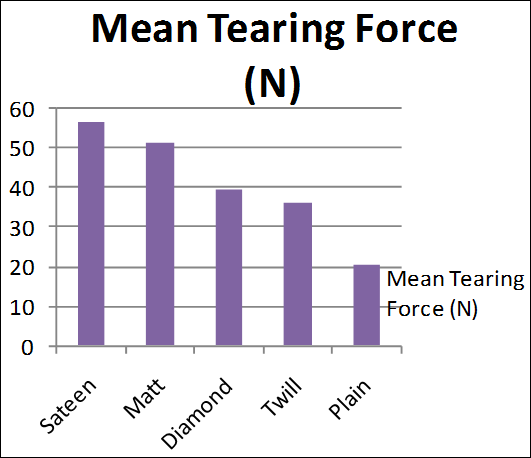
Fig. 36. Mean Tearing Force for Weft.
5. Discussions
The behavior of woven fabrics under tearing loads is quite different from their other behavior like tensile loading. In case of tensile loading, all the yarns in the direction of loading share the load; in tear loading only one, two, or at most a few yarns share the load. So the fabric structures play very important roles in determining the fabric tear strength. Restricted movement of yarn during loading of tight constructions will show low tearing strength. That’s why plain weaves show low tearing strength. Loose, open constructions allow more freedom for the yarns to move and group together, thus presenting bundles of yarns to the tearing load; in consequence, the tear strength is high. So designs which have groups of yarns woven together, such as matt & loose structure like sateen weaves will have high tear strengths.
6. Conclusion
To sum up, it is obvious that, tearing behavior of a fabric is vastlyreliant on the weave designs. Elevated interlacement causes superior crimp in the load bearing direction may lead to lower breaking strength whereas too much bigger floats also cause lower breaking strength because of looser structure.
References
- Zeydan M. (2010), "Prediction of Fabric Tensile Strength By Modelling the Woven Fabric, Woven Fabric Engineering", PolonaDobnikDubrovski (Ed.), Sciyo Publisher.
- Kabir, R. B. (2013), "Tensile & Tearing Strength Test of Different Weave Structures", 1st ed., Lambert Academic Publishing, Germany.
- Lord P R, Mohamed M H (1994), Weaving: Conversion Yarn to Fabric, Merrow Publishing Co. Ltd, England.
- Scelzo W A, Backer S, and Boyce M C (1994), Mechanistic Role of Yarn and Fabric Structure in Determining Tearing Resistance of Woven Cloth, Part 1: Understanding Tongue Tear, Textile Research Journal, 64 (5), pp. 291-304.
- Malik, Z. A., Hussain T., Malik M. H., and Tanwari A. (2011), "Selection of Yarn for the Predefined Tensile Strength of Cotton Woven Fabrics", Fibers and Polymers, Vol.12, No.2, 281-287.
- Majumdar, A.; Ghosh, A.; Saha, S.S.; Roy, A.; Barman, S.; Panigrahi, D.&Biswas, A. (2008), "Empirical Modelling of Tensile Strength of Woven Fabrics" Fibers and Polymers, Vol.9, No.2, 240-245.
- P Angappan and R Gopalakrishnan (2007) Textile Testing, 8th edition, p.293,Tamil Nadu, S.S.M. Institute of Textile Technolgy.
- J E Booth (2009) Principles of Textile Testing, 3rd edition, p.436, Oxford, Butterworth Heinemann Ltd.
- S Dhamija, C Manisha (2007) "Tearing Strength of cotton fabrics in relation to certain process and loom parameters", Indian journal of fibers and textile research, Vol. 32, pp. 439-445.
- Chellamani K P, Arulmozhi&Vittopa M K, (2000). Compact spinning-The spinning of the future, Asian Textile Journal, 9(9), pp. 30-33.
- Ishtiaque-SM, Salhotra-KR, Kumar (2003), "A Study of effect of spinning process", Asian Textile Journal, 12(12), pp. 74-82.
- Dash J R, Ishliaque S M & R Alagirusamy (2002), "Properties and processibility of compact yarns", Indian Journal of Fiber & Textile Research, Vol. 27; pp. 362-368.
- Skelton, J., (1980), Tearing behaviour of woven fabrics, in J.W.S. Hearle et al " Mechanics of flexible fibre assemblies", Sijthoff&Noordhoff, p. 243.Hu, J. and Chan,Y.F., (1998), Effect of Fabric Mechanical Properties on Drape, Textile Research Journal, 68 (1), 57-64.