Development of Theories and Methods on Water-Inrush Risk Evaluation and Grouting Reinforcement Technique for Lower Group Coal Seam Floor in Northern China Typed Coalfields
Wang Hua1, 2, 3
1Institute of Mine Construction, Tiandi Science and Technology Co., Ltd., Beijing, China
2Beijing China Coal Mine Construction Engineering Co., Ltd., Beijing, China
3National Engineering Laboratory for Deep Shaft Construction Technology in Coal Mine, Beijing, China
Email address
Citation
Lihui Li, Tao Wen, Xiaohua Wang, Da Liu. The Transformation of the Chinese Economic Development Mode Promoted by Science and Technological Input. International Journal of Economic Theory and Application. Vol. 3, No. 2, 2016, pp. 26-39.
Abstract
In view of frequent accidents of water inrush from the floor of Lower Group Coal Seam (hereafter, LGCS for short) in North China Type coal Field (hereafter, NCTC for short) in China, Chinese scientific and technical workers did a lot of research work in theories and methods on water-inrush risk evaluation and grouting reinforcement technique for the coal seam floor, they have achieved fruitful research results. This paper firstly made a systematical introduction of the history and present situation of theories and methods on water-inrush risk evaluation and grouting reinforcement technique for coal seam floor in China, and elaborated the main contents of water-inrush coefficient method, theory of original position tension crack and the zero position failure, the theory of strong infiltrating channel, etc, respectively; secondly, it introduced the development course of boreholes layout for large-area grouting reconstruction of the aquifer in coal bed floor, which has progressed from fan-shaped boreholes opening in underground roadway, directional boreholes opening in underground roadway, to directional boreholes opening on the surface; thirdly, it introduced the application status of geophysical techniques (such as electronic resistivity CT method, detection layer with seismic wave, radio wave penetration tomography, transient electromagnetic, and so on) in exploring the effect of large-area grouting reconstruction of the floor of LGCS; fourthly, it pointed out that, based on further study of the mechanism of water-inrush from coal seam floor, studying the interaction between grout and floor strata of LGCS, using the way of directional borehole opening on the surface to grouting reconstruction of the floor strata of LGCS, and adopting the comprehensive geophysical techniques to detect and evaluate the water inrush risk of LGCS floor before and after grouting reconstruction will be the development trends of water prevention and control in LGCS floor in the future.
Keywords
Northern China Typed Coalfield, Lower Group Coal Seam, Water Prevention and Control Technology, Development Trend, Confined Water of Ordovician Limestone, Pre-grouting, Directional Borehole
1. Introduction
The Northern China typed coalfield has a wide distribution in China, extending from the Yinshan Mountains in the north to the Qinling Mountains and Dabie Mountains in the south, bordering in its west region the Helan Mountains and adjoining in the east region the Yellow Sea and the Bohai Sea [1-2] (Fig. 1). Its distribution centers Shanxi Province, including coalfields located in more than ten provinces, municipalities and autonomous regions, such as Beijing, Hebei, Henan, Shandong, Shanxi, western of Inner Mongolia, Shaanxi, Ningxia, Jiangsu, Anhui, etc. The characteristic of the coalfield is widespread, mass coal-bearing stratum, large reserves and so on. The total area of coal bearing is about 1.5×105 km2, in which the total coal resources is 556.99 billion tons within 1000 meters in depth, 930.24 billion tons within 1500 meters in depth and 1 370.656 billion tons within 2000 meters in depth [2-3]. The coal-bearing rock series of NCTC is a set of Permo-Carboniferous strata. Because Upper Ordovician, Silurian, Devonian and Lower Carboniferous strata are commonly missing in this area, coal measure strata cover directly on the thick carbonate formation of Middle Ordovician (or Cambrian) [4-5]. NCTC is one of the most important coal industry bases in China, of which coal production is more than 60% of the total national output [6], playing an important role in the national economic development.
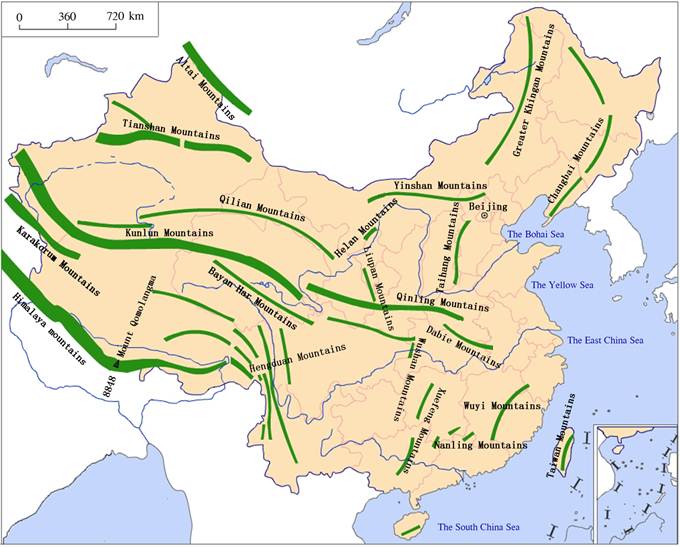
● The map is from https://www.baidu.com.
Fig. 1. The map of major mountains in China.
In China, with the continuous exploitation of coal resources, mining depth is increasing; therefore, most of the mining depths in coal mines have gone deep 800 ~ 1000 m, ushering in a period of deep mining in coal mining [2]. In North China typed coal field, main mining coal seams are from Upper Shihezi Formation of Upper Permian (P2s), Lower Shihezi Formation of Lower Permian (P1x) and Shanxi Formation of Lower Permian (P1s) to Taiyuan Formation of Upper Carboniferous (C3t), lower group coal seams [7-12] (also known as A group coal seams in Huainan Coal Field [13-16] of China) have been mined. One of the coal mines, Suncun Coal Mine of Shandong Energy Xinwen Mining Group, has a mining depth downward 1501 m, becoming the deepest coal mine in China and even in Asia [2]. There are usually hydraulic connection between several thin limestone layers of Upper and Middle Carboniferous and their underlying Ordovician limestone, their water contents are all stronger; and in addition, the distances between them and lower group coal seams are usually shorter [4]. The Ordovician limestone is thick (where karst cracks develop and water contents are strong), also close to the lower group coal seams (generally, the thicknesses of strata between them are 12~60 m)[18], because of these factors, a large amount of water bursting accidents happened in the process of mining the lower group coal seams in many coal mines. According to incomplete statistics, from 1927 to 1985, 17 outsize floor water bursting accidents (of which the amount of gushing water was more than 1.0 m3/s) happened in the North China Typed Coalfields [3]; Since 1955, more than 2000 water bursting accidents have happened (of which the headwaters were all karst water from the thin layers of limestone in coal measure strata and the basal Ordovician limestone) including 220 mine flooding accidents. The economic loss was hundreds of billions yuan; and casualties were more than 8000 [19]. Among these accidents, in Handan-Xingtai Mining Area alone, since 2000, 10 floor water inrush accidents of Ordovician limestone aquifer have occurred (9 of which in working faces, one of which in the roadway driving face [20]) caused great economic losses and casualties. Major water inrush accidents of Ordovician limestone aquifer in North China Typed Coalfield are shown in table 1.
According to the source of water bursting in coal mines in China, water disasters can be divided into surface water disaster (including the water disaster of old mined-out area), alluvial soil water disaster, sandstone-type aquifer water disaster and limestone karst water disaster, accounting for 4.9%, 1.4%, 1.4% and 92.3% of all the accidents respectively [39]. A large number of water inrush data show that most water inrush sources of the limestone karst type are floor aquifer, especially during the course of mining lower group coal seams in the North China typed coal field, where serious water inrush accidents are related to the underlying Ordovician limestone aquifer. Therefore, before mining lower group coal seam, assessing and predicting the water inrush risk, and taking relevant measures for water prevention and control of working faces, are of great significance for the safe production in coal mine.
2. Development of Theories and Methods on Water-Inrush Risk Evaluation for Coal Seam Floor
2.1. The Research Status in Foreign Countries
In 1944, Weigle Florence from Hungary first put forward the concept of relative water-resisting layer of coal seam floor [40]. He pointed out that water inrush from seam floor is not only related to the thickness of water-resisting layer, but also related to water pressure; Water-inrush condition is restricted by the thickness of relative water-resisting layer; The thickness of relative water-resisting layer is the ratio of equivalent thickness of water-resisting layer and water pressure. At the same time, he suggested that water inrush would not happen in the case that relative water-resisting layer thickness is greater than 1.5 m/atm, and 80% ~ 88% of floor water bursting accidents are caused where relative water-resisting layer thickness is less than this value. Thus, the concept of "if the relative thickness of water-resisting layer is greater than 2.0 m/atm, the floor water bursting will not happen" has been referenced in many countries that mine coal seam over the confined aquifer. During this period, the former Soviet Union scholar, B. Slesarev looked upon the coal floor as a beam with both ends fixed under uniformly loading, and combined the Strength Theory to deduce the calculation formulas of theoretical safe water pressure of coal seam floor [41].
From 1960s to 1970s, the Hungarian National Mining Technical Appraisal Committee added the concept of relative water-resisting layer to Mining Safety Procedures, and gave the corresponding regulations and instructions according to different conditions of each mine [42-43]. Subsequently, the scholars in former Soviet Union and Yugoslavia began to study the effect of relative water-resisting layer [44-46], including the influence on the thickness of water-resisting layer from stress change caused by goaf, and the relationship between water and rock structure, etc [47-48].
From 1970s to the end of 1980s, in many countries researchers of rock mechanics studied the damage mechanism of the floor while they studied the stability of pillars. The most representative are C. F. Santos and Z. T. Bieniawski, they based on the improved Hoek-Brown strength criterion of rock, introduced the concept of critical energy release and analyzed the bearing capacity of the coal seam floor [41].
Table 1. Statistics of great disasters of Ordovician limestone water-inrush in Northern China Typed Coalfield [4,19,21,38].
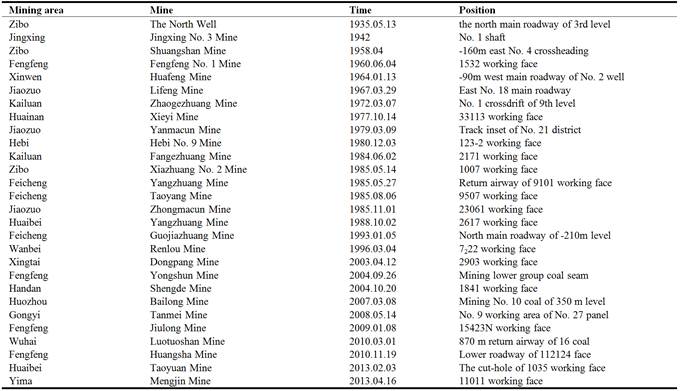
Table 1. Continued.
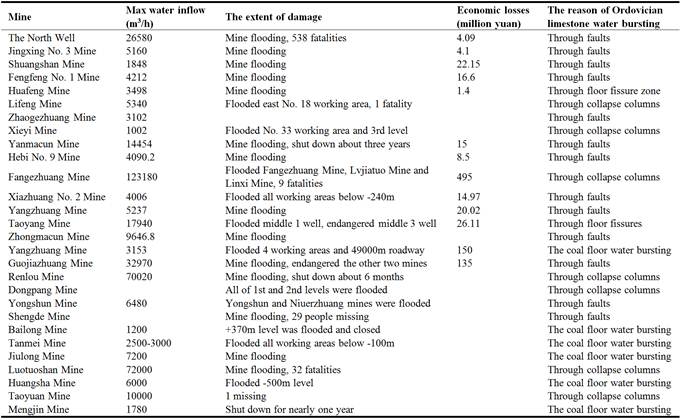
2.2. The Research Status in China
Compared with other countries, China started the study of water inrush very late. It is after the founding of the People's Republic of China that such kind of research work emerged. Since then, with the development of the coal industry, the theoritical research and its application in the study of water-inrush from coal floor developed rapidly in China. E.g., in the 1950s, the Slesarev’s Water Inrush Theory was introduced in China to predict water inrush. From 1960 s to 1970 s, Chinese mainly prospected for hydrogeological conditions of mines, and then through studying the hydrogeological conditions, carried out the empirical decision-making for prevention and control of coal mine water hazards. The work, the basis for the prevention and control of coal mine water disaster, belongs to the research category of conditioned hydrogeology. Because research means were relatively backward at that time, the development of this subject was restricted. The prototype of conceptual model of water inrush from coal seam floor was basically formed during this period. It encompasses many concepts, such as floor prevention layer and original initial induction height, etc. Since the 1980s, in China, many scholars have been devoted to the research of prevention and control of floor water, and have done the systematic research works in predicting and forecasting water disaster, the mechanism of water-inrush, technology of water prevention and control, etc. Indebted to all these researches, the research on floor water-inrush become frontier science of mining-intrigued combined effect of lithology, structure and geological environment of (regional tectonic stress field, seepage field, temperature field and water-physical reaction field, etc.) of surrounding rock. Generally, Chinese scientific workers’ researches on floor water inrush mechanism of many years have been cagorized into the following major theories and methods:
2.2.1. Water-Inrush Coefficient Method
In the 1960s, Chinese scholars summarized a large number of water inrush cases, counted the data of water pressures and floor water-resisting layer thicknesses which are closely related to the water inrush in four mining areas, namely Fengfeng, Jiaozuo, Zibo and Jingxing. Then they selected two principal factors, i.e. water pressure of aquifer and thickness of water-resisting layer, from many factors based on two aspects of promoting and preventing water inrush, and advanced the concept of water inrush coefficient, established its empirical formula (formula (1)), and gave the critical value of water inrush coefficient for each of the above mentioned four mine regions (Table 2), then the critical value of water inrush coefficient was quickly spread and applied all over China. The threshold (or critical value) of water inrush coefficient was based on the observed data of a large number of water inrush statistics, determined to be 0.06 ~ 0.07 MPa/m. In accordance with the critical value, we determine whether the coal seam is threatened by water risk or not. According to the actual situation, different critical water inrush coefficient was selected in different mining areas.
(1)
Where,
TS —— critical water inrush coefficient, MPa/m;
P —— water pressure, MPa;
M —— thickness of floor water-resisting layer, m.
In the 1970s, Hydrological geological scholars of Xi’an Branch of China Coal Research Institute, by referring to the Hungarian’s experience and considering the damage of the underground pressure to the coal floor, amended the formula of water inrush coefficient (formula (2)).
(2)
Where, CP is the depth of floor fractured zone (m).
For a long time, the water inrush coefficient method has played an important role in water prevention and control in coal mines in China. It is not only written into the relevant regulations, but still widely used in some fields today [23,49,50].
Table 2. Critical water inrush coefficients of some mine districts in Northern China Typed Coalfield [49].
Mine district | Fengfeng | Jiaozuo | Zibo | Jingxing |
Critical water inrush coefficient TS (MPa/m) | 0.066~0.076 | 0.060~0.100 | 0.060~0.140 | 0.060~0.150 |
2.2.2. Theory of Original Position Tension Crack and Theory of Zero Position Failure
Wang Zuoyu [51-52] (1988) put forward theory of original position tension crack and theory of zero position failure on coal seam floor rock mass movement.
Theory of original position tension crack argues as follows: firstly, the movement of floor rock mass is controlled by the combined effect of ground pressure and water pressure in mining coal above confined aquifer, and ground pressure and water pressure are active forces which generally lead to floor water-inrush in mining working face; secondly, under the combined effect of ground pressure and water pressure, influence range of working face on coal seam can be divided into three sections: compression section by advancing pressure (I), expansion section by pressure relief (II) and stable compression section by pressure after mining coal (III); thirdly, bottom-up original position tension cracks of rock mass will develop in compression section by advancing pressure. The theory describes the forming process of original position tension crack, and reasonably explains the mechanism of floor water inrush in mining coal above the confined aquifer.
Theory of zero position failure argues: in transition stage from I section to II section, the state of construction rock mass of coal floor initiates qualitative change, and the rock mass in the state of compression will sharply release pressure. Because storage energy in rock mass storage is greater than the energy that rock mass can bear, it will release residual elastic strain energy with the type of brittle failure, and new balance of rock energy will be formed, leading to the zero position failure of the stope floor rock mass. Theory of zero position failure on construction rock mass of coal floor reveals the formation law of bottom-up zero position failure and its maximum depth of floor rock mass in mining. It shows that in II section, because time-space conditions of original position tension crack and zero position in releasing pressure are both at the same maximum value of damage; the most dangerous section in the process of mining is formed.
The theory adopts the theory of plastic slip line field to research criterion of zero position failure working face floor, main influence parameters and their selection, and analyse according to them. Research findings include mining supporting force of roof dead weight stress field is an essential pre-requisite causing floor failure, plastic failure width of pillar is an essential condition of controlling floor maximum failure depth; inner friction angle of floor rock mass is an essential element influencing failure, of which the angle is main index reflecting mechanical strength of rock mass [53].
2.2.3. Theory of Strong Infiltrating Channel
The Institute of Geology of Chinese Academy of Sciences [54] (1992) proposed the theory of strong infiltrating channel. The theory argues whether or not water inrush from floor occurs is the crux of water inrush channle’s formation. It includes two cases: one is that the floor has water inrush channels connecting the coal seam and the underlying aquifer. When they are uncovered by the colliery excavate engineering, water inrush accident can be intrigued; the other is that the floor has not the natural water inrush channel, but under the common action of engineering stress, crust stress and underground water, along the weak links of the floor rock mass structure and hydrogeological structure, the rock mass yields to deformation, disintegration and failure, forms a new strongly penetrating infiltrating channel, as the result, inducing water inrush. The former belongs to the primary channel water inrush, the latter belongs to regenerate or secondary channel water inrush. The theory attaches great importance to the influence of weak planes of geological structure (including faults and joints) on water inrush, but lacks proper study on the influence of mining and water pressure on water inrush, especially the influence of mining pressure on it[24,41].
2.2.4. Theory of Thin Board Model
In the 1990s, academician Liu Tianquan, Zhang Jincai, et al. [55] of Beijing Research Institute of Coal Mining of China Coal Research Institute (CCRI) put forward the concept that floor strata are made up of mining water-flowing fractured zone and water-resisting zone, and used elastic solution of the semi-infinite body on the certain length under vertical uniform load, and combined the Mohr-Coulomb Strength Theory and Griffith Strength Theory to calculate the floor maximum mining damage depth. On this basis, they used Thin Plate Theory and Elastic-plastic Theory to deduce the calculation formula on limiting water pressure that the floor could bear. Theory of thin board model is mainly suitable for thin board with the ratio between thickness and width less than 1/5 ~ 1/7. In practice, this condition is hard to meet, so its popularization and application are limited [41].
2.2.5. The "Five Figures and Double Coefficients" Method and the "Vulnerable Index" Method
Xi’an Branch of China Coal Research Institute, and Kailuan Coal Mining Administration, et al. [56] (1995) put forward the "five figures and double coefficients" method. It is a kind of method for evaluating water inrush risk of coal seam floor, mainly using "five figures", "double coefficients", "three level discrimination" to evaluate the risk. The "five figures" refers to the thickness contour map of floor protective layer, the failure depth contour map of floor protective layer, the effectivethickness contour map of floor protective layer, the contour map of water head over the coal floor, evaluative map of mining coal above confined aquifer; The "double coefficients" refers to the coefficient of construction pressure and the coefficient of water inrush; The "three level discrimination" refers to the three indicators to be used with "double coefficient" to discriminate the probabilty of the water inrush occurance, water inrush form and change of water quantity: I level discrimination is an indicator to discriminate that in the working face straight-through type water inrush will inevitably happen; II level discrimination is a indicator to discriminate the possibility that in working face non-straight-through type water inrush happens and water inrush forms; III level discrimination is a indicator to discriminate the water quantity change in working face that has been discriminated by n level discrimination in which water inrush will happen.
Wu Qiang et al. [58-62] (2007-2013) successively put forward a series of new practical methods to evaluate the risk of floor water-inrush. The methods includ the principal controlling index system construction, the artificial neural network (ANN) vulnerable index method based on geographic information system (GIS), the weight of evidence vulnerable index method based on GIS, the logistic regression vulnerable index method based on GIS, the analytic hierarchy process (AHP) vulnerable index method based on GIS, etc. The "vulnerable index" method is guided by the theory of multi-source information integration with GIS as the operation platform, based on analyzing the main controlling factors of water-inrush from coal floor, through data collection, analysis and processing, to establish thematic layer map of the main control factors. It applies composite and superposition principle to multi-source geological data, and uses the modern linear or nonlinear mathematical methods (such as ANN, the weight of evidence vulnerable index method, the logistic regression method, AHP method, etc.), through inversion recognition or learning training on the model, to determine "contribution" or "weight" of each main controlling factor of the floor water-inrush in the complex water inrush process, and makes a forecast and evaluation model for floor water inrush; Then it analyzes the histogram of water-inrush vulnerable index frequency of each unit in the research area, finally generates scientific division and forecast evaluation for the vulnerability of floor water-inrush.
The "five figures and double coefficients" method and the "vulnerable index" method have been written into Water Prevention Regulation of Coal Mines [49].
2.2.6. The Key Stratum (KS) Theory
According to the layered structure characteristics of coal floor rock mass, academician Qian Minggao, Li Liangjie et al. [63] (1996) built the key stratum (KS) theory of water inrush mechanism from stope floor.
They proposed to find the highest strength stratum in floor strata as the key stratum of floor, and look on the key stratum as a thin board, this will be good to meet the basic requirements of thin board theory, and can use the thin board strength theory to study the floor failure. The thin board model is the most suitable model for bedding ore body. The theory is on the base of the advanced distance of working face while floor water inrush happens (usually 30 ~ 40m) and thickness of water-resisting layer (generally 20 ~ 30m) can not meet the basic requirements of the thin board model theory, that is to say, the ratio between thickness and width of board plate is less than 1/5 to 1/7, they thought: strata of coal measures have a layered structure characteristic, and each layer thickness is generally 2 ~ 6m, a maximum bearing capacity stratum can be found under mining damage zone and above aquifer, which is called the key stratum; if the floor key stratum is seen as a thin board, apparently, it is good to meet the basic requirements of the thin board model theory. Therefore, under the conditions of fault structure, the key stratum structure model of both sides of the fault can be simplified into a rectangular board with three sides clamped and one side free or three clamped edges and one simply supported edge under uniform load, thus research of water inrush mechanism of fault can be changed into research of relative displacement of key stratum and the failure law of key stratum structure model. Key strata theory is the development of board model and perfection of the thin board model theory.
2.2.7. The View of Rock-Water-Stress Relations
Li Kangkang and Wang Chengxu [64] (1997) attributed the problem of floor water inrush to the relations among the rock (floor sandshale), water (floor confined water) and stress (mining stress and underground stress), which is termed as the view of rock-water-stress relations. They proposed to use the critical index of water inrush, namely the ratio of water stress and the minimum principal stress of floor water-resisting layer bearing, as the criterion of water inrush. If the critical index of water inrush is greater than 1, the floor water inrush will occur.
2.2.8. The Similarity Theory Method
Academician Qian Minggao, Li Liangjie, et al. [65] (1997) put forward the similarity theory method, and used three-dimensional model and plane stress model and simulated water pressure of aquifer by water to carry out the similar material tests of water-inrush from coal floor in longwall faces. The results show that: (1) Without fault, the O-X type failure will occur in the floor under the water-pressure of the confined aquifer, and the passage of water-inrush will be most probably formed at the point of intersection of "O" and"X"; (2) The cause for water-inrush through fault is that the difference of upward relative displacements happens at the key strata of both sides of fault under the confined water pressure, and when it is most probably that the maximum difference of displacement occurs, it is more likely that the accident of water-inrush happens; (3) The fill in the fault zone is eroded by the confined water while the accident of water-inrush occurs; (4) whether or not water inrush happens through fault is related to working face layout and advancing direction; And in gapping fault water inrush is more likely to happen than in compression fault. Similarity theory method proves that key stratum (KS) theory of water inrush mechanism is correct.
Gong Peilin, Hu Yaoqing, et al. [66] (2005) put forward the similarity theory on coupling of solid and liquid, and developed solid-liquid coupling similarity ratio of some typical simulation materials and made 3D solid-liquid coupling similarity simulation experiment table. They studied the law for deformation and breakage of coal floor on mining above aquifer by the experiment table, and obtained the dynamic change process of stress and deformation of coal floor. It provides theoretical foundation for coal mining above aquifer.
Jiang Yaodong, Zhao Yixin, et al. [67] (2013) adopted bi-directional load similarity simulation experiment table and the confined load simulator with a series of spring group to analyze the mechanism of floor fracture to induce water inrush at mining working face above aquifer, and gained the time-space evolution characteristics of stress and displacement field in floor strata during the process of mining.
The above-mentioned researches improve and perfect the similarity theory method of water-inrush from floor of the lower group coal.
2.2.9. The Information Theory of Floor Water-Inrush
Aiming at characteristics of water inrush from coal seam floor, Jin Dewu, Ma Peizhi, et al. [68] (1998) put forward random-information method to predict water inrush problem and set up information criterion.
Academician Song Zhenqi, et al. [69] (2003) put forward the dynamic information theory of water inrush from coal floor. They pointed out that the information basis of forecasting and controlling the floor water inrush includes: (1) The information of folds, faults and the characteristics of original tectonic stress field in mine field; (2) The information of the bottom position of water-abundant thick layer limestone and the distribution of confined karst water; (3) The information of magnitude, distribution characteristics and key influential factors (such as mining depth, mining height, length of working face, etc.) of supporting pressure in stopes; (4) The state of water-inrush accident prevention facilities, such as mine drainage capacity, mine storage capacity, and so on.
2.2.10. The "Down Three Zones" Theory and the "Four Zones" Theory of Coal Seam Floor
After years of comprehensive observation of the internal part of coal seam floor under mining conditions, and combined with various research results of simulation experiments, computer analysis, etc, Li Baiying [70] (1999) put forward the "Down Three Zones" theory. He thought there are three zones in coal floor from top to bottom, namely mining damage zone (h1), complete water-resisting zone (h2) and water conductive zone (h3). As the mining design, the thickness of safe waterproof rock pillar of coal seam floor (ha) (Fig. 2) should accord with the following condition:
ha≥h1 + h2 + h3
The "Down Three Zones" theory plays an important role in evaluating safe mining and directing water disaster prevention and control in the lower coal seam, and has been written into Regulations of Pillar Leaving and Coal Mining Under Building, Water, Railway and Main Shaft and Tunnel, guiding the work of water prevention and control in coal mines.

Fig. 2. Sketch of waterproof rock pillar design for coal floor.
But the "Down Three Zones" theory is mainly used in studying the water-inrush condition without any faulted structure in stope floor; therefore, since it was put forward, it has not developed further.
AcademicianSong Zhenqi, Shi Longqing [71] (2000) pointed out that two main reasons hinder the development and extensive application of the "Down Three Zones" theory: Firstly, there are unclear concepts in the theory, such as "floor damage zone", "complete rock stratum zone"; therefore, each zone has no uniform determination method; Secondly, the mechanical essence of each zone development is not sufficiently uncovered, leading to the theoretical calculation formula of each zone thickness is not clear. Based on modern damage mechanics theory and fracture mechanics theory, they put forward the concept that mining floor can be divided into four zones, that is, the zone destroyed by underground pressure, new damaged zone, originally damaged zone and zone of pressure water inducing height. And they deduced the calculation formulas of the zone destroyed by underground pressure, new damaged zone and originally damaged zone respectively. On the basis of the"four-zone"theory, the occurance of the water inrush from mining floor can be determined.
2.2.11. The Theory of Preferred Plane
According to the theory and method of preferred plane on hydrogeology and engineering geology by Luo guo-yu and Yan Chang-hong, Ni Hong-ge and Luo guo-yu [72-74] (2000) put forward the theory of preferred plane on water-inrush from coal floor. They thought geological structures of coal measures strata is the key to control water disaster, in numerous geological structures, preferred fracture plays an important role in controlling water disaster. In the process of mining lower group coal seam, most of the large delayed water inrush from covered Ordovician limestone aquifer in coal seam is mainly due to: the larger fault fracture zone with wide width near the excavation space of coal seam usually form the "barrier" for stress and strain redistribution ofsurrounding rock, which leads to the increase of the gradients of stress, produces tensile cracks, connect the Ordovician limestone aquifer, make fault become a water-abundant fault; Surrounding rock between the fault and the floor of mining coal seam floor generates a stress concentration that causes shear deformation to enormously aggravate the dislocation of discontinuous surface in rock mass, resulting in the ineffective water-preventive coal-rock pillar; consequently, the water inflow increases sharply from the slow flow, forming large delayed water inrush.
In addition, Wang Chengxu [75] (1997) used the structural mechanics method and the theory of ultimate bending moment to make the formula for calculating effective thickness of floor water-resisting layer above Ordovician limestone aquifer; Gao Yanfa [76] (1998) used the method of multivariate statistical regression to gain the statistical formula of floor damage depth; Feng Qiyan, Chen Qihui [77] (1998) adopted finite element program, ADINA, to calculate the damage depth of the floor, they concluded that the floor damage shape is saddle-shaped without fault; Feng Qiyan, Yang Tianhong, et al. [78] (2006) set up numerical simulation of the mining failure formation of thin coal seam floor based on the theory of the flow and damage coupling by using F-RFPA2D (Coupling System of Flow & Solid in Rock Failure Process Analysis), and simulated the course of fracture instability, crack expanding and water inrush from coal seam floor under the condition of mining, and predicted the position of the water outburst; Fu Pingjie, Wei Jiu-chuan, et al. [79] (2015) utilized multifactor fuzzy clustering analysis to determine the key factors and weight of the influential factors of water-burst, established the model of water inrush from seam floor, divided the research area into different partitions based on risk of water inrush from coal floor, and determined the risk level; Through deeply and systematically analyzing typical floor water-inrush examples in mining the large depth working faces of lower group coal seam above Ordovician confined aquifer in Handan-Xingtai Mine District of North China Coalfield, based on time-space 4D structural concept and time-space evolution process, Zhao Qingbiao, Wu Qiang, etc. [80] (2015) put forward a water burst mechanism of"divided period and section burst"at coal seam floor, which explains that the floor water inrush is the results of a variety of "mechanism" working together in mining the large depth working faces above high confined aquifer.
The above theory and method have been widely used in the production practice, and achieved good results. However, due to the wide distribution of North China typed coalfields in China, the complex geological conditions, more influence factors involved in LGCS floor water inrush, there are still many theoretical problems which need to be studied further.
3. The Technology of Large-Area Grouting Reinforcement for Floor Aquifer of Lower Group Coal Seam
Considering the lower group coal seam is underlied with the confined aquifer of strong water yield, the space between coal seam and aquifer is small, and water flowing fractured zone of coal seam floor is widely developed, large-area grouting reconstruction for its floor aquifer should be the most effective way to prevent and control floor water inrush.
The large-area grouting reinforcement technology of aquifer in coal seam floor pours directly a great quantity of grout into aquifer which threatens coal mining through the grouting holes arranged according to rational design. The grout concretion body will be filled into the karst-fissures and cracks of aquifer, changing the aquosity of aquifer, rendering the strong aquifer into the weak aquifer or water-resisting layer. At the same time, the floor is reinforced to block the supply channels of aquifer. However, the "large area" is different from a small-area aquifer pre-grouting, as the latter is often used in construction of shafts [4].
The large-area grouting reinforcement technology of aquifer in coal bed floor can be employed by practicing many patterns of borehole layout, such as surface vertical holes, underground fanshaped holes, underground directional holes, surface directional holes.
3.1. The Development History of Grouting Reinforcement Technology for Local Underground Aquifer by Ground Vertical Hole
The history that grouting method is applied to transform the water permeability of stratum is not too long, only a little more than 200 years, dating from 1802 when Charles·Berigny from France poured clay grout and hydraulicity gypsum into the strata to improve the stability and permeability of the strata for the first time. In 1885, Tiejens from Germany used the method of pouring cement grout into strata to prevent water inrush as digging vertical shaft, and achieved success. From 1899 to 1904, 88 mines in France, Germany and Belgium had adopted the method of grouting to cut-off water, and all had brought about the good effect. But it was until 1905 that the Bethune Company literally began to adopt machinery to stir grout and mechanical pump to improve grouting pressure. In 1907, the United States began to use grouting method in the mining operations. Since then, the grouting method to cut-off water with cement grout has been widely used in the world.
In China, the grouting technology started in the early 1950s. In the coal industry, the walling grouting technoloy was firstly used to seal shafts’ leaking in Hegang Mining Area and Jixi Mining Area in the Northeast China, Zibo Mining Area in Shandong Province in East China. In 1955, the working face pre-grouting method was used in constructing the vertical shaft of Zhangzhuang Coal Mine in Xinwen Mining Area of Shandong Province resulting in the good effect of water plugging. In the late 1950s, the surface pre-grouting was used in Xuecun Coal Mine of Fengfeng Mining Area with the good effect that water shutoff rates of main shaft and auxiliary shaft both reached 96.3%. Another example is Licun Coal Mine of Jiaozuo Mining Area where water shutoff rates of the vertical shaft even reached 99.6%. By the end of 1990s, according to the incomplete statistics, the number of shafts built by the surface pre-grouting method had amounted to 195.
3.2. Grouting Reinforcement for Large-Area Floor Aquifer of Lower Group Coal Seam by Ground Vertical Holes and Underground Fanshaped Holes
Feicheng Mining Area is the birthplace of large-area grouting reconstruction technology for floor aquifer. In 1984, Yu Shuchun put forward grouting reconstruction technology for coal floor aquifer. By 1991, a set of large-area grouting reinforcement techniques for coal seam floor aquifers had been basically developed and used in many mining areas. The development of the technology can be mainly divided into five stages [4]:
3.2.1. The Stage of Preliminary Experiment
In 1984, aquifer grouting tests were made in 9312 working face and 9314 working face in Dafeng Coal Mine, and 9507 working face in Taoyang Coal Mine of Feicheng Mining Bureau. The vertical grouting borehole was drilled from ground area corresponding with the first weighting section of the working face to the underground fifth limestone layer in coal measure strata, and cement grout was poured into the fifth limestone layer. In every working face one borehole is drilled to be poured in with 40~60t cement each. Although in the tests no practical engineering effect was achieved, it dawned with an overall new thinking on the active control of the mine water disaster generating a major breakthrough for prevention and treatment of water disasters of the coal working face;
3.2.2. The Stage of Improving the Construction Technolgoy of Grouting Borehole
Grouting test was made in 9306 working face in Yang Zhuang Coal Mine, adopting well-distributed and densely-arraged borehole layout. The inclined grouting boreholes were drilled from middle rail roadway of 9306 working face to the floor fifth limestone layer; and the temporary grouting station was built underground; and the neat cement grout was poured into the floor fifth limestone layer. In the test, 21 grouting boreholes were drilled, and about 500t cement was poured into the layer. In the process of mining, the water inrush didn’t take place.
3.2.3. The Stage of Improveing the Grouting Technolgy
The grouting technology combining the ground facilities with underground facilities: on the ground the grouting station was built and the grouting borehole was drilled; while under the ground the grouting pipes were laid down. Ground grouting station was composed of slurry pump, bulk cement container, slurry agitating pool, grouting pool, etc. The cement slurry made by ground grouting station would be impressed into grouting boreholes in working face through slurry pump, grouting borehole and underground grouting pipes, then the coal floor aquifer was grouted and reconstructed. After grouting technology had been improved, the technology of large-area grouting reconstruction for floor aquifer of lower group coal seam was widely applied in Feicheng Mining Bureau. By the end of 1991, 59 working faces had undertaken grouting reconstruction, relesing coal reserves of 5.009 million tons from the threat from floor aquifer, causing the safe mining of the coal of more than 3.6 million tons, and producing a good effect.
3.2.4. The Stage of Improving the Grouting Material
In 1991, Feicheng Mining Bureau and Beijing Mine Construction Research Institute of China Coal Research Institute cooperated and determined to use clay-cement grout as the material for aquifer grouting reconstruction. Then the aquifer grouting tests were made in 9206 working face and 99208 working face in Dafeng Coal Mine of Feicheng Mining Bureau. The results showed that, as the grouting material for transforming limestone aquifer, the clay-cement grout is much better than pure cement grout because it not only costs low, but also has good effect.
3.2.5. The Stage of Further Improving the Grouting Technology
Since 1991, aquifer grouting reconstruction technology has been applied in many mining areas in North China typed coal field, and the technology has attempted the constant improvement oriented to the specific problems in the practical work.
Since the 21st century, the shallow coal resources have almost been exhausted in main mining areas in North China after many years of mining; hence it is urgent to exploit the deep lower group coal seams. Therefore, we need to do more work on studying the water-resisting property of the upper strata of Ordovician limestone aquifer and the corresponding grouting reconstruction technology in order that a large number of lower group coal resources can be set free. Zhao Weidong et al. [87] (2005) analyzed and evaluated the grouting reconstruction effect of floor limestone aquifer of 25111 working face and its mining safety by water releasing test after grouting reconstruction; After analyzing the water yield property of karst aquifer in Ordovician Fengfeng Group in Dongpang Coal Mine of Xingtai Mining Group, Nan Shenghui [88] (2010) put forward a test plan for grouting reform of the 40-meter-thick stratum of the upper part of Ordovician limestone. After grouting, the average outflow rates of boreholes reduced by 74 percent. Wu Jiwen, et al. [89-90] (2014) used electronic resistivity CT method and logging with seismic wave to analyze and evaluate the floor grouting reinforcement effect and aquifer grouting reconstruction effect of II615 working face in Hengyuan Coal Mine of Wanbei Coal-Electricity Group Co., Ltd.; In 2014, Jiulong Coal Mine of Fengfeng Mining Group Co., Ltd. used underground grouting method to make grouting reinforcement for floor weak tectonic belt and water-abundant thin-layer limestone area of 15248 working face, and commissioned Anhui HuiZhou Geology Security Institute Co., Ltd. to comprehensively detect the floor before and after grouting to ensure the safety in mining [91].
At present, underground fanshaped-hole arrangement is usually adopted in large-area grouting reconstruction for floor aquifer of lower group coal seam. The requirements of boreholes design are that each borehole must penetrate through the main fissures in the depth of the design reconstruction strata. Therefore, the vertical depth of the inclined borehole must be greater than or equal to the design depth of the floor aquifer grouting reinforcement [4], as is shown in figure 3.
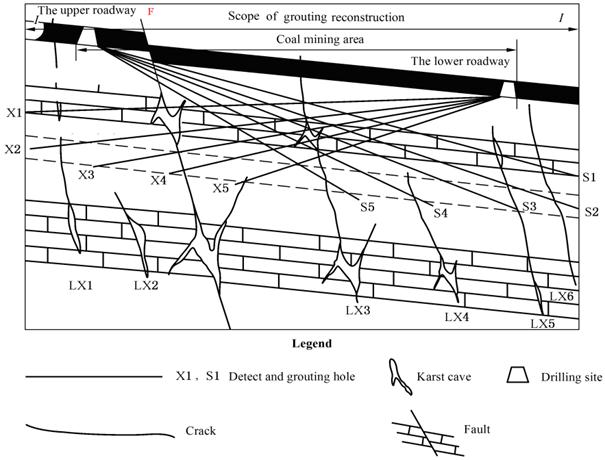
Fig. 3. Profile of boreholes layout to grout the LGCS floor.
3.3. Directional Drilling Grouting for the Coal Floor Aquifer of Lower Group Coal Seam
3.3.1. The Brief Introduction to Directional Drilling Technology
The directional borehole (or well) is operated according to the advance design deviation azimuth and the axis shape of the borehole (or well).
In the late 19th century, directional drilling technology originated in the United States. At that time, the researchers did not consider stabilizing drilling tools to control borehole trajectory, so borehole test showed that those "vertical boreholes" were not vertical.
In the 1930s, the needs of exploration and exploitation of the undersea oil fields prompted the development of the directional drilling technology, awakening people to consciously using borehole bending phenomenon in realizing directional drilling and drilling directional borehole to fulfil the aim of oil exploration and exploitation.
The first recorded case of directional well was that two directional wells were drilled in California in the United States of America in 1930s. The two directional wells were both obliquely drilled from Huntington Beach to the bottom of the sea. Then, in order to exploit the petroleum below the Sunnyside Cemetery in America Signal Hill Oilfield, a few more directional wells were drilled.
In 1934, in order to exploit the petroleum below the seashore, the former Soviet Union drilled a few directional wells from the coast of Caspian Sea in Baku to the bottom of the offshore. In the same year, a directional relief well was drilled in Conroe Oilfield in Texas in the United States.
By the early 1950s, the former Soviet Union and France had developed turbine drill; however, in the meantime, America Smith Tool Company developed the helicoid hydraulic motor. In the 1960s, Polycrystalline Diamond Compact drill bit turned out to promote the development of technology by using turbine drill to drill the directional well. In the 1970s, many western countries began to widely adopt helicoid hydraulic motors (or screw drill) in drilling deep directional wells, at that time, many companies in the United States have begun to produce their own helicoid hydraulic motors, such as Smith, Baker, and so on. Nowadays, the specifications and production of the screw drill have formed a complete system. In the 1980s, in order to more accurately control and know well the trajectory of borehole in directional drilling process, people began the wide implementation of MWD (Measurement While Drilling) technology and CAD (Computer Aids Drilling) technology. The application of screw drill and two such technologies led the development of the directional drilling technology in exploitation of petroleum and nature gas into the mature stage.
In China, directional drilling began in the 1950s; and China is the 3rd country who can drill directional horizontal well, following the United States and the Soviet Union. At that time, the directional drilling technology was mainly used in exploration of oil and gas fields. In the early days after the foundation of the People's Republic of China, China introduced a few ring measurement and gyro orientation borehole inclinometers. In 1956, China’s first directional well was drilled in Yumen Oilfield of Gansu Province in Northwest China. In the late 1970s, with the rapid development of Marine directional drilling technology in China, 12 directional cluster wells were drilled on a offshore drilling platform in Bohai Gulf. By 1982, 316 directional wells had been drilled all over China. Particulary in the same year, in drilling a directional well in Jiangyou County of Sichuan Province in Southwest China, the actual well trajectory basicallly accorded with design trajectory; and the depth of the well was 2720m, and the horizontal displacement of the well was 1080m. From 1985 to 2000, China prompted the cooperation between domestic large oil fields, petroleum universities and petroleum research institutes to pool their wisdom and strength for joint research to seek the key techniques, such as directional wells, cluster wells, horizontal wells, sidetracking horizontal wells, etc. The extremely remarkable achievements had been made, greatly narrowing the gap between China and the advanced world in directional drilling technology. In that duration, offshore oil fields benefited by making good use of cooperation with foreign countries, making significant breakthrough in large displacement wells technology, and creating a number of world records of highly-displacement well in 1997.
3.3.2. Directional Drilling Grouting Reinforcement for the Coal Floor Aquifer of Lower Group Coal Seam
Horizontal directional drilling technology used in grouting reconstruction roadway surrounding rock in coal mine began in 2012. In order to improve the stabilities of surrounding rock and safety of supporting structure of a deep roadway in Xinhu Coal Mine of Huaibei Mining Group, Institute of Mine Construction, Tiandi Science and Technology Co., Ltd. (Beijing China Coal Mine Construction Engineering Co., Ltd.), Huaibei Mining Group, Anhui University of Science and Technology and other units jointly carried out the research on "the key technologies of pre-grouting reinforcement of the surrounding rock of 1000-meter-deep roadway by L typed borehole from ground" to make grouting reinforcement of the central pump room and electric power substation of shaft bottom. Firstly, they drilled two vertical holes on the ground; then in the bottoms of two vertical holes, they were divided into three horizontal branch holes (i.e., 1# vertical hole became L1 horizontal branch hole, and 2# vertical hole divided into L2 and L3). The overall design scheme of grouting construction is shown in figure 4. It realized ground pre-grouting reinforcement of 1002.5m vertical depth and 200m horizontal length, the grouting volume of single hole reaching 1459m3 in whipstocking section and 955.5 m3 in horizontal drilling section. It had significantly reduced the drilling hole amount, and significantly increased the grouting scope and effect of single hole, ensuring the surrounding rock stability of deep mine roadways [94-95].
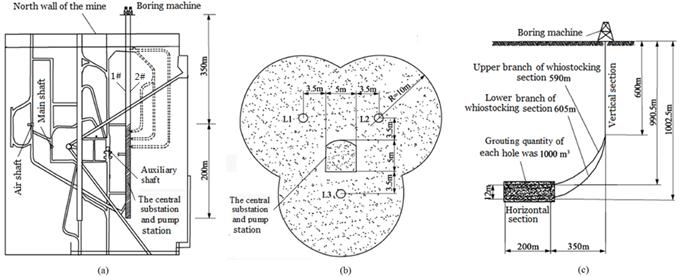
Fig. 4. Overall design scheme of the grouting reinforcement.
(a) Layout diagram of the grouting holes;
(b) Sketch map of the target positions of horizontal holes;
(c) Sketch map of the trajectory of 2# grouting hole
In 2013, two drill sites were built in 11151 working face in Zhaogu No. 1 Coal Mine of Jiaozuo Mining Industry Group in Henan Province in Central China. Zhaogu No. 1 Coal Mine used directional drilling technology and equipment to make pre-grouting reinforcement test of coal floor, and totally five directional boreholes had been drilled of which the longest horizontal hole was up to 135m. The diagram of the structure of directional borehole for drilling is shown in figure 5. The good effect of coal floor grouting reinforcement had been achieved, enriching and perfecting the means of preventing and controlling water disasters from coal floor aquifer, and made a major breakthrough in the in-advance prevention and control of water disasters from coal floor aquifer [96]. Subsequently, Horizontal directional drilling technology were used in grouting reinforcement of the floor aquifer of LGCS in 15445 working face and 15445N working face in Jiulong Coal Mine of Fengfeng Mining Industry Group and the III631 working face in Zhuzhuang Coal Mine of Huaibei Mining Group. They had all achieved the aim of water prevention and control, ensuring safety in mining the LGCS [97-99].
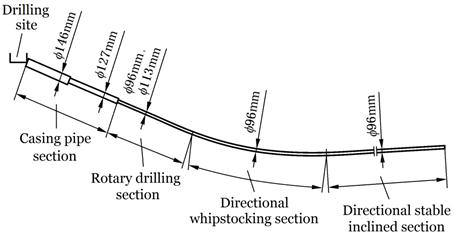
Fig. 5. Diagram of directional borehole opening in underground roadway to grouting reinforcement the LGCS floor.
From 2015 to 2016, Institute of Mine Construction of Tiandi Science and Technology Co., Ltd. used TD2000/600 type full hydraulic top drive drilling rig which they themselves developed and horizontal directional drilling technology to conduct the grouting reinforcement for floor Daqing limestone aquifer (the vertical distance between the aquifer and Daqing coal seam is about 115m) of Daqing coal seam (which belongs to the lower group coal seams) in 216 mining area in Xin’an Coal Mine of Fengfeng Mining Industry Group, and blocked off the underground watercourse (including many conductivity structures, such as concealed collapse post, fault, fracture, etc.). The design included one main borehole (vertical borehole the depth of which is 530m) and 10 directional branch boreholes (Fig. 6). The horizontal distance between every two adjacent boreholes was 40 m. And in horizontal section of No. 1-4 directional branch hole, a secondary directional branch hole (which was along the main joint tendency) was drilled every 200 meters, a total of 5 secondary branch holes were drilled; and each secondary branch hole was in Daqing limestone stratum, the parameters of each secondary branch hole are shown in table 3. The actual drilling length of horizontal section of No. 1-5 branch hole was 984 m, and the 12032 m3 cement groutwas poured into the hole, its water cement ratio was 3:1.
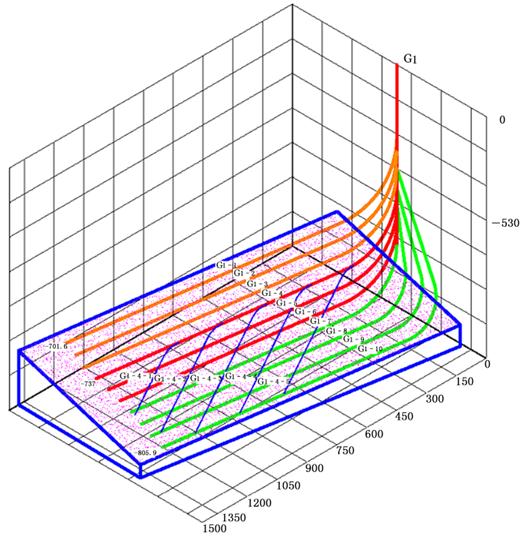
Fig. 6. Diagram of directional borehole opening on the surface to grouting reinforcement the LGCS floor.
Table 3. Engineering quantity schedule of exploring hydrogeological condition and grouting reinforcement to the LGCS floor in 216 Mining Area of Xin’an Coal Mine.
Hole No. | Directional section Length/m | horizontal section Length/m | Section length/m |
1-1 | 530-973 | 973-1953 | 1423 |
443 | 980 |
1-2 | 530-982 | 982-1952 | 1422 |
452 | 970 |
1-3 | 530-995 | 995-1955 | 1425 |
465 | 960 |
1-4 | 530-1012 | 1012-1962 | 1432 |
482 | 950 |
1-5 | 530-1035 | 1035-1985 | 1455 |
505 | 950 |
1-6 | 530-1056 | 1056-1996 | 1466 |
526 | 940 |
1-7 | 530-1077 | 1077-2007 | 1477 |
547 | 930 |
1-8 | 530-1103 | 1103-2023 | 1493 |
573 | 920 |
1-9 | 530-1136 | 1136-2056 | 1526 |
606 | 920 |
1-10 | 530-1169 | 1169-2103 | 1573 |
639 | 934 |
4. Conclusions
(1). Because of the wide distribution of the Northern China typed coalfield in China and the different geological and hydrogeological conditions of coal mines, at present, any one of water inrush theories has its certain limitations and particular conditional requirements for its implementation, and it is difficult to completely solve the problem of floor water inrush as mining lower group coal seam; therefore, floor water inrush accidents still happen occasionally, and study of theories and methods on water-inrush risk evaluation for coal seam floor must be strengthened in China.
(2). At present, cement grout and clay-cement grout are usually used in large-area grouting reconstruction for coal floor aquifer of lower group coal seam. The interaction mechanism of grout, stratum (lithology) and groundwater (water chemical characteristics) is not sufficent; The research of the influence on grout diffusion radius by pressure of grout, pressure of underground water, flow velocity of underground water, viscosity coefficient of underground water is not enough either. The design of the slurry ratio and grouting boreholes parameters has often been subject to the subjective and random judgement, lacking rationality and efficiency. In this case, researchers need to do more work on studying grout material, the interaction mechanism of grout-stratum-groundwater and the main factors that affects grout diffusion.
(3). The application of directional drilling technology in coal field has gradually grown mature. As for water inrush risk of lower group coal seam in the Northern China Typed Coalfield, using directional drilling technology to carry out large-area grouting reinforcement for the aquifer in coal seam floor is development trend in the prevention and control of the mine water;
(4). The application of comprehensive geophysical prospecting methods should be strengthened in detecting and evaluating the risk of coal floor water inrush, and evaluating the grouting reinforcement effect of coal floor aquifer to ensure safety in mining lower group coal seam.
References
- YAN Shu, SHI Xianxin, CHEN Mingsheng. Issues on probing depth of hydrogeological electrical magnetic method for exploration of North China coalfield [J]. Coal Science and Technology, 2006, 34 (12): 5-8. (in Chinese).
- SUN Wenjie, WANG Yawei, LI Xuekui, et al. Analysis on hydrogeological classification and water inrush accidents in North China coal mines [J]. Coal Engineering, 2015, 47 (6): 103-105. (in Chinese).
- WU Qiang, CHEN Youming, TIAN Kaiming, et al. The research of "para-three-dimensional" numerical model for forecasting water inflow in mine in the coalfield of North China [J]. Earth Science-Journal of China University of Geosciences, 1992, 17 (1): 87-94. (in Chinese).
- YU Shuchun. Large-area grouting reconstruction technology of aquifer in coal bed floor [M]. Beijing: China Coal Industry Publishing House, 2014. (in Chinese).
- WU Qiang, JIN Yujie. Decision system for prevention and control of mine water in North China coal mines [M]. Beijing: China Coal Industry Publishing House, 1995. (in Chinese).
- HAN Yong, LIU Yunfang, LIU Demin, et al. Study on the hydrogeochemistry and isotope characteristics of Ordovician groundwater in typical coalfield of North China—taking Yanzhou as an example [J]. Journal of North China Institute of Science and Technology, 2014, 11 (2): 28-34. (in Chinese).
- LIAN Huiqing, YANG Wuyang, ZHAO Dongyun. The study of influential factors of Ordovician limestone water inrush under floor in following coal of Zhangcun mine [J]. Journal of North China Institute of Science and Technology, 2010, 7 (1): 4-7. (in Chinese).
- Li Nana, Shi Longqing, Liu Meijuan. Study on lower group coal seams mine water inflow prediction in Xinyi Coal Mine [J]. Coal Geology of China, 2010, 22 (2): 22-27. (in Chinese).
- YIN Hui-yong, WEI Jiu-chuan, WANG Ying, et al. Risk evaluation of water inrush from seam floor during mining of lower group in Zhaizhen coal mine [J]. China Mining Magazine, 2009, 18 (11): 97-99. (in Chinese).
- CHEN Xiang-ling, WEI Jiu-chuan, SUI Yan-gang. Evaluation of the floor water inrush risk during mining of lower group of coal seams in Yanzhou Mining Area [J]. Journal of Shandong University of Science and Technology (Natural Science), 2008, 27 (2): 10-13. (in Chinese).
- SHI Shaozhou. Application of Visual MODFLOW in Hydrogeological Exploration—A case study of hydrogeological exploration in lower coal group early stage winning district of Xinyi Coal Mine, Shandong [J]. Coal Geology of China, 2007, 19 (S2): 24-27. (in Chinese).
- MA Peizhi. Criterion models of mining under high pressure and groundwater controlling countermeasures for lower group coal of Northern China type coal field [J]. Journal of China Coal Society, 2005, 30 (5): 608-612. (in Chinese).
- HUANG Hui, JIANG Fawen, HAN Biwu, et al. Comprehensive detection analysis on the reason of abnormal gas blow-out from the drilling hole through the floor limestone of A group coal seam in Huainan mining area [J]. Journal of China Coal Society, 2013, 38 (11): 1988-1992. (in Chinese).
- CHENG Aimin. Study of floor water hazard controlling for steep A coal seam group mining [J]. Coal Geology & Exploration, 2004, 32 (S1): 161-163. (in Chinese).
- ZHANG Shizhen, LIU Guijian, YAN Zhicao, et al. Geochemical features of REE in coal group A in Dingji Coal Mine, Huainan [J]. Coal Geology of China, 2012, 24 (1): 7-9. (in Chinese).
- LIU Guanxue, TANG Yongzhi, HE Youju, et al. Precaution of karsts water of deep part of seams in group A in Xie'er Mine [J]. Coal Mining Technology, 2002 (S2): 18-21. (in Chinese).
- WU Jialin, XIN Delin, ZHANG Jianping. Innovation and development of underground coal mining technology [J]. Coal Engineering, 2014, 46 (1): 4-8. (in Chinese).
- LI Qiming, ZHAI Lijuan, FU Yaojun, et al. A study on coal mining aquifer destruction mode in North China Typed Coalfields [J]. Coal Geology of China, 2012, 24 (7): 38-43.
- Lower group coal seams water bursting (inrush) mode and characteristics in North China Type Coalfields [J]. Coal Geology of China, 2015, 27 (8): 38-42. (in Chinese).
- Zhao Qingbiao, Jiang Qinming, Gao Chunfang. Study on floor water inrush mechanism of deep seam in Hanxing Mining Area [J]. Coal Science and Technology, 2016, 44 (3): 117 - 121, 176. (in Chinese).
- BU Changshen, ZHANG Xicheng, YIN Wancai, et al. Inundation in the North China Typed Coalfields and the status quo of its protection [J]. Geological Review, 2001, 47 (4): 405-410.
- LI Huaqi. Water prevention and control in mines [M]. Beijing: China Coal Industry Publishing House, 2012. (in Chinese).
- MENG Zhaoping, GAO Yanfa, LU Aihong. Theory and method of water inrush risk assessment in coal mine [M]. Beijing: China Science Publishing House, 2012. (in Chinese).
- FAN Shukai. The coal floor water bursting evaluating and countermeasure of south coalfields in North China-A case study of Xinji No. 2 Mine [Ph. D. Thesis] [D]. Beijing: China University of Mining & Technology, Beijing, 2012. (in Chinese).
- XU Liangcai, GUO Yinghai, HUANG Xinlei, et al. Introduction to main water inrush types and the technologies of water prevention and control of coal mines in China [J]. Safety in Coal Mines, 2011, 42 (1): 53-56. (in Chinese).
- ZHAO Suqi, GUO Qiwen, CHEN Xiaoguo. Quick drilling and grouting technology for heavy water disasters of collapse post in Renlou Mine, Wanbei Mining Bureau [J]. Zhongzhou Coal, 1997 (5): 15-17. (in Chinese).
- YUE Weizhen. Analysis on water inrush and rapid treatment of 15423N working face in Jiulong Coal Mine [J]. Safety in Coal Mines, 2011, 42 (6): 145-147. (in Chinese).
- SHAO Hongqi, WANG Wei. Using double-liquid grouting method to quickly building the water resistance wall for sealing water-inrush roadway [J]. Safety in Coal Mines, 2011, 42 (6): 145-147. (in Chinese).
- GUAN Yongqiang. Analysis on Cause of Water Rush in the 112124 Driving Working Face of Huangsha Mine [J]. Coal and Chemical Industry, 2015, 38 (1): 24-27. (in Chinese).
- SHAO Dongmei. Study on dissolution test of Ordovician carbonate rock in North China Typed Coalfields [M. S. Thesis] [D]. Xi’an: Xi’an Branch, China Coal Research Institute, 2009. (in Chinese).
- GUANG Yongqiang, WANG Tieji, YUN Weizhen. A study on the Niuerzhuang Coalmine Ordovician limestone water flooding governing [J]. Coal Geology of China, 2006, 18 (3): 37-39. (in Chinese).
- YUN Weizhen, WANG Tieji. Aggregate material technology for Ordovician limestone water treatment in Niuerzhuang Mine [J]. Coal Science and Technology, 2007, 35 (2): 36-38.(in Chinese).
- ZHANG Jianying, ZHANG Dongying. Identification of water-inrush source at 11011 working face and study on dynamic water grouting in high pressure in Mengjin Mine [J]. China Coal, 2015, 41 (6): 110-113.(in Chinese).
- MOU Lin. Water inflow prediction for water-burst induce by floor tectonic in coal-seam under water pressure [J]. Coal Mining Technology, 2015, 20 (2): 85-89. (in Chinese).
- FEI Xin-qing, JIANG Shao-yong. Water bursting mechanism analysis and manipulation in Tanmei Coal Mine of Henan Dayugou Coal Group [J]. Journal of Henan Polytechnic University (Natural Science), 2012, 31 (4): 392-396. (in Chinese).
- SHI Longqing, BU Changshen, WEI Jiuchuan, et al. Theory and technology of karst water prevention and control for Ordovician limestone in the North China Typed Coalfields [M]. Beijing: China Coal Industry Publishing House, 2015. (in Chinese).
- LI Yongjun, LI Xiaoming, XU Haitao. Theory and method of karst water hazard prevention and control for Permo-Carboniferous Coalfields in North China [M]. Beijing: China Coal Industry Publishing House, 2015. (in Chinese).
- China Coal mine safety net. Assembly of water-inrush accident cases in China coal mines [EB/OL]. http://www.mkaq.org/html /2014/10/05/274380_3.shtml, 2014.10.05. (in Chinese).
- GAO Yujie. Based on the coal energy structure is still necessary choice in China's energy development. [DB/OL]. http://www.coalchina.org.cn /page/info.jsp?id= 13923, 2009.10.27. (in Chinese).
- KONG Hailing, WANG Luzhen, YANG Min. Analysis of harmfulness of water-inrush in the floor of a coal mine [J]. Journal of xuzhou Institute of Technology (Natural Sciences Edition), 2009, 24 (3): 17-19. (in Chinese).
- SHI Long-qing. Summary of research on mechanism of water-inrush from seam floor [J]. Journal of Shandong University of Science and Technology (Natural Science), 2009, 28 (3): 17-23. (in Chinese).
- Chunlin LI. Micromechanics modeling for stress-strain behaviour of brittle rocks [J]. Int. J. for Numerical and Analytical Methods in Geomechanics, 1995, 19 (1): 331-334.
- M. Cai, H. HORH. A constitutive model and FEM analysis of jointed rock masses [J]. Int. J. for Rock Mech. Min. Sic. & Geomech. Abstr. 1993, 30 (4): 351-359.
- Tom Clem, Leslie Smith. A hierarchical model for solute transport in fractured media [J]. Water Resources Research, 1997, 33 (4): 1763-1783.
- Olivier Bour, Philipper Davy. Connectivity of random fault networks following a power law fault length distribution [J]. Water Resources Research, 1997, 33 (7): 1567-1583.
- Shemin GE. A governing equation for fluid in rough fractures [J]. Water Resources Research, 1997, 33 (1): 53-61.
- Alberto Carpinterl. A catastrophe theory approach to fracture mechanics [J]. Int. J. of Fracture, 1990, 44 (1): 57-69.
- Yonghong Zhao. Crack pattern evolution and a fractal damage constitutive model for rock s [J]. Int. J. for Rock Mech. Min. Sic, 1998, 35 (3): 349-366.
- State Administration of Work Safety of P. R. China, State Administration of Coal Mine Safety of P. R. China. Water prevention regulation of coal mines [S]. Beijing: China Coal Industry Publishing House, 2009. (in Chinese).
- State Coal Industry Bureau. Regulations of pillar leaving and coal mining under building, water, railway and mail shaft and tunnel [M]. Beijing: China Coal Industry Publishing House, 2000. (in Chinese).
- WANG Zuoyu. Theory of original position tension crack on coal seam floor rock mass movement [J]. Hebei Coal, 1988 (3): 29-31. (in Chinese).
- WANG Zuoyu. Theory of zero position failure on coal seam floor rock mass movement [J]. Hebei Coal, 1988 (4): 36-39. (in Chinese).
- WANG Zuoyu. Analysis calculation of Max depth of floor zero position failure zone [J]. Coal Science and Technology, 1992 (2): 2-6. (in Chinese).
- Institute of Geology, Chinese Academy of Sciences. The research on mechanism of water-inrush from karst water in coal mines in China [M]. Beijing: Science Press, 1992. (in Chinese).
- ZHANG Jincai, ZHANG Yuzuo, LIU Tianquan. Rock mass permeability and coal mine water inrush [M]. Beijing: Geological Publishing House, 1997. (in Chinese).
- LI Xin. Technological achievements of the second phase of industrial test for comprehensive prevention and control of karst water in Ordovician limestone engineering in North China type coal field [J]. Coal Geology & Exploration, 1995 (6): 50. (in Chinese).
- WANG Guangdi. The development of prediction and evaluation methods on mine water-inrush in China [J]. Inner Mongolia Coal Economy, 2016 (1): 31-32. (in Chinese).
- WU Qiang, ZHANG Zhilong, MA Jifu. A new practical methodology of the coal floor water bursting evaluating I—The master controlling index system construction [J]. Journal of China Coal Society, 2007, 32 (1): 42-47. (in Chinese).
- WU Qiang, ZHANG Zhilong, ZHANG Shengyuan, et al. A new practical methodology of the coal floor water bursting evaluating II —— the vulnerable index method [J]. Journal of China Coal Society, 2007, 32 (11): 1121-1126. (in Chinese).
- WU Qiang, XIE Shuhan, PEI Zhenjiang, et al. A new practical methodology of the coal floor water bursting evaluating Ⅲ: the application of ANN vulnerable index method based on GIS [J]. Journal of China Coal Society, 2007, 32 (11): 1121-1126. (in Chinese).
- WU Qiang, WANG Jinhua, LIU Donghai, et al. A new practical methodology of coal seam floor water burst evaluation IV: the application of AHP vulnerable index method based on GIS [J]. Journal of China Coal Society, 2009, 34 (2): 233-238. (in Chinese).
- WU Qiang, ZHANG Bo, ZHAO Wende. A new practical methodology of coal seam floor water burst evaluation V: the comparison study among ANN, the weight of evidence and the logistic regression vulnerable index method based on GIS [J]. Journal of China Coal Society, 2013, 38 (1): 21-26. (in Chinese).
- Li Liangjie, Qian Minggao, Li Shugang. Mechanism of water-inrush through fault [J]. Journal of China Coal Society, 1996, 21 (2): 119-123. (in Chinese).
- LI Kangkang, WANG Chengxu. The technique measuring on the stress of rock mass used in the study of the mechanism of the water-inrush from coal floor [J]. Coal Geology & Exploration, 1997, 25 (3): 31-34. (in Chinese).
- LI Liangjie, QIAN Minggao, YIN Youquan. Stope Research on the tests of water-inrush from floor simulated by similar materials [J]. Coal Geology & Exploration, 1997, 25 (1): 37-40. (in Chinese).
- GONG Peilin, HU Yaoqing, ZHAO Yangshen, et al. Three- dimensional simulation study on law deformation and breakage of coal floor on mining above aquifer [J]. Chinese Journal of Rock Mechanics and Engineering, 2005, 24 (23): 4396-4402. (in Chinese).
- ZHAO Yixin, JIANG Yaodong, LV Yukai, et al. Similar simulation experiment of bi-directional loading for floor destruction rules in coal mining above aquifer [J]. Journal of China Coal Society, 2013, 38 (3): 384-390. (in Chinese).
- JIN Dewu, MA Peizhi, WANG Yanfu. Random-information simulation and forecast of water inrush through coal seam floor in mining area of Northern China [J]. Coal Geology & Exploration, 1998, 26 (6): 36-39. (in Chinese).
- SONG Zhenqi, JIANG Yujing, YANG Zenfu, et al. Basic research on dynamic information of forecasting and controlling for major accidents in coal mine [M]. Beijing: China Coal Industry Publishing House, 2003. (in Chinese).
- LI Baiying. "Down Three Zones"in the prediction of the water inrush from coal bed floor aquifer theory, development and application [J]. Journal of Shandong Institute of Mining and Technology (Natural Science), 1999, 18 (4): 11-18. (in Chinese).
- SHI Long-qing, SONG Zhenqi. Theoretical study of four-zone division of mining floor [J]. Journal of Jiaozuo Institute of Technology (Natural Science), 2000, 19 (4): 241-245. (in Chinese).
- NI Hongge, LUO Guoyu. Study on the mechanism for water transportation and rock mass stability controlled by preferred plane in underground mining [J]. Journal of Engineering, 2000 (3): 316-319. (in Chinese).
- NI Hongge, LUO Guoyu. Study on the mechanism of preferred plane of water hazard in coal mine [J]. Journal of China Coal Society, 2000, 25 (5): 518-521. (in Chinese).
- NI Hongge, LUO Guoyu. A study of the mechanism of hazards controlled by preferred plane in underground mining [J]. Geology Review, 2000, 46 (1): 71-78. (in Chinese).
- WANG Chengx. The method of structural mechanics for studying the gushing from coal floor [J]. Coal Geology & Exploration, 1997, 25 (S1): 48-50. (in Chinese).
- GAO Yanfa. Statistical analysis on damage depth of coal seam floor [J]. Coal Geology & Exploration, 1988, 16 (1): 38-41. (in Chinese).
- FENG Qiyan, CHEN Qihui. Dynamic simulation on damage depth of coal seam floor in mining [J]. Mine Pressure and Roof Management, 1998 (3): 71-73. (in Chinese).
- FENG Qiyan, YANG Tianhong, YU Qinglei, et al. Numerical simulation on water-inrush from the seam floor based on the coupled analysis of seepage and damage [J]. Journal of Safety and Environment, 2006, 6 (3): 1-4. (in Chinese).
- FU Pingjie, WEI Jiuchuan, XIE Daolei, et al. Risk evaluation of water inrush from seam floor based on multifactor fuzzy clustering analysis [J]. Coal Technology, 2015, 34 (1): 163-166. (in Chinese).
- ZHAO Qingbiao, ZHAO Xinnan, WU Qiang, et al. Water burst mechanism of"divided period and section burst"at deep coal seam floor in North China type coalfield mining area [J]. Journal of China Coal Society, 2015, 40 (7): 1601-1607. (in Chinese).
- CONG Shan. Design and construction of curtain grouting project for water plugging in mine [M]. Beijing: Geological Publishing House, 2011. (in Chinese).
- CAI Shenghua, HUANG Zhiyong, DONG Jianjun, et al. Grouting method [M]. Beijing: China Water and Power Press, 2006. (in Chinese).
- DENG Jingsen, CHEN Xueyun, XIONG Houjin, et al. In-situ chemical grouting reinforcement material [M]. Beijing: China Water and Power Press, 2010. (in Chinese).
- ZHANG Yongcheng. Grouting technology [M]. Beijing: China Coal Industry Publishing House, 2012. (in Chinese).
- WANG Hao. Research on grouting reinforcing and support in mining roadway with soft cracked surrounding rock [M. S. Thesis] [D]. Xuzhou: China University of Mining and Technology, 2008. (in Chinese).
- LIU Xueshan. New type of grouting material——clay-cement grout [J]. Mine Construction Technology, 1991 (1): 17-18. (in Chinese).
- LI Chang-qing, ZHAO Wei-dong Li Yun-xia. Grouting transform technique of aquifer in coal bed floor in Hanwang Coal Mine [J]. Journal of Henan Polytechnic University (Natural Science), 2005, 24 (1): 18-21. (in Chinese).
- NAN Shenghui. Technical feasibility of grouting reform for upper part of Ordovician limestone in Xingtai and Handan coal mining areas [J]. Coal Geology & Exploration, 2010, 38 (3): 37-40. (in Chinese).
- WU Jiwen, SHEN Shuhao, ZHAI Xiaorong, et al. The wave velocity detection and evaluation of the effect of grouting reinforcement in coal seam floor [J]. Geophysical and Geochemical Exploration, 2014, 38 (6): 1302-1306. (in Chinese).
- WU Jiwen, ZHAI Xiaorong, ZHANG Haichao, et al. The electronic resistivity CT detection and research of holes and roadways on the mining effect of floors after grouting reinforcement and reconstruction of aquifers [J]. Progress in Geophysics, 2015, 30 (2): 920-927. (in Chinese).
- LI Chun- cai, DU Shu’an. Recovery working face pre-mining baseboard grouting reinforcement technology application [J]. Coal and Chemical Industry, 2014, 37 (11): 70-73. (in Chinese).
- WEI Xuejing, ZHAO Xiangze. Directional drilling technology and operation guide [M]. Beijing: Petroleum Industry Press, 2012. (in Chinese).
- LIU Weipeng. Study on application of high-precision directional drilling technology in the CBM mediato [M. S. Thesis] [D]. Beijing: China University of Geosciences (Beijing), 2012. (in Chinese).
- YUAN Hui, DENG Yun, PU Chaoyang, et al. L type borehole ground grouting reinforcement technology of surrounding rock in deep mine roadway [J]. Coal Science and Technology, 2014, 42 (7): 10-13. (in Chinese).
- AN Xuliang. Application of surface pre-grouting with L-style drill-hole in underground roadway reinforcement engineering [J]. Coal Mining Technology, 2014, 19 (1): 56-59. (in Chinese).
- LI Quanxin, SHI Zhijun, FANG Jun. Drilling technology and equipment for pre-grouting reinforcement directional borehole in coal floor [J]. Metal Mine, 2013 (9): 126-131. (in Chinese).
- ZHAO Pengfei, ZHAO Zhang. Ordovician Limestone floor inrush water advance treatment technology with surface horizontal branch borehole grouting [J]. Coal Science and Technology, 2015, 43 (6): 122-125. (in Chinese).
- CHAI Zhenjun. Research on application of level fixed well technology in control of Ordovician limestone water [J]. Hebei Coal, 2013 (2): 17-19. (in Chinese).
- Analysis of water inrush causes in Ⅲ 631 working face water and integrated control [J]. Shandong Coal Science and Technology, 2014 (9): 153-154, 157. (in Chinese).
Biography
Wang Hua obtained MSc and PhD from Anhui University of Science and Technology, Huainan, China. At present, he is an associate professor of Institute of Mine Construction, Tiandi Science and Technology Co., Ltd., and is the director of editorial department of Mine Construction Technology, Beijing, China. And he is a member of Chinese Sub-society for Soft Rock Engineering and Deep Disaster Control, a life member of the American Association for Science and Technology, and a member of editorial board of the Scientific World Journal. His research interests cover hydrogeology, engineering geology, safety engineering, mining engineering, geophysical exploration, grouting technology, etc. |