Enhancing Oil Recovery Using Formulated Surfactants Extracted from Oil Palm and Local Coconut Coir Containing Lignosulfonate
Sagala Farad1, 3, 4, Muhammad A. Manan1, Hussein Kisiki Nsamba2, 3, Wan Mohammad Kamal Bin Wan Jaafar1, Kabenge Isa4,
Wasswa Joseph4
1Department of Petroleum Engineering & Renewable Energy, Skudai, Johor, Universiti Teknologi Malaysia (UTM), Malaysia
2Section of Industrial Chemistry, department of Chemistry, College of Natural Sciences, Makerere University, Kampala, Uganda
3Invention plus limited, Kampala, Uganda
4Department of Agricultural and Biosystems Engineering, College of Agricultural and Environmental Sciences, Makerere University, Kampala, Uganda
Email address

(S. Farad)
Citation
Sagala Farad, Muhammad A. Manan, Hussein Kisiki Nsamba, Wan Mohammad Kamal Bin Wan Jaafar, Kabenge Isa, Wasswa Joseph. Enhancing Oil Recovery Using Formulated Surfactants Extracted from Oil Palm and Local Coconut Coir Containing Lignosulfonate. Engineering and Technology. Vol. 3, No. 2, 2016, pp. 53-60.
Abstract
Surfactants have all along been used to reduce the interfacial tension (IFT) between oil and water to overcome the trapping phenomena that causes oil to be trapped. The costs of surfactants on the other hand derived from petroleum-based source are costly. This study aims to extract lignin compound from oil palm empty fruit bunch (EFB) and coconut fiber by soda pulping technique, and characterize it by using Fourier Transform Infrared Spectroscopy (FTIR). Three formulations from each lignin with lowest IFT were evaluated for their performance in remobilizing residual oil through oil displacement experiments. All experiments were performed at room temperature and pressure. For the formulation containing oil palm lignin, the formulation containing (SDBS-E4) gives the highest oil recovery (4.10% of original oil in place) while for the formulation containing coconut fiber, formulation containing (SDBS-C5) gives the second highest oil recovery (3.30% of original oil in place). The results show that lignin based surfactants have a high potential to recover residual oil. Therefore, surfactants obtained from palm oil and coconut coir can be used as alternative sources in surfactant flooding application given the challenging oil prices and the cost of the petroleum based surfactants which is high.
Keywords
Black Liquor, Oil Palm, Coconut Fiber, Lignin, Surfactant, Enhanced Oil Recovery
1. Introduction
After primary and secondary production from an oil reservoir, about 65% of the original oil-in-place (OOIP) still remains trapped. This oil trapping is due to the capillary forces holding the oil in place (Morrow & Mason, 2001). Enhanced Oil Recovery (EOR) processes typically are the tertiary stage applied in the third phase of reservoir-oil producing life with the aim of increasing production (Dawe, 1991). The main objectives of this process is to improve displacement efficiency by reducing the capillary and interfacial force, and to improve the sweep efficiency by reducing the mobility ratio between injected and displaced fluid (Wang, 2002). Chemical EOR methods such as surfactant flooding involve injection of chemicals (surfactants) to improved oil recovery (Lake & Venuto, 1990). The unique features of surfactant for use in this process are their ability to reduce the oil-water interfacial tension and alter reservoir wettability (Schramm & Marangoni, 2000). Surfactant can cause the remaining oil in place to be mobilized and allows it to move to producing Wells (Donaldson, Chilingarian, & Yen, 1989). Many type of surfactants have been used and the most popular surfactants used this method are petroleum-based surfactants (Bera, Ojha, Mandal, & Kumar, 2011); Various techniques and methods have been used by researchers in this field to develop the best surfactant formulations for the EOR process (Reed & Healy, 1977); A good surfactant slug should achieve lowest IFT to mobilize residual oil and create oil bank where both oil and water flow as continuous phases, form homogeneous Micro emulsion when a mixtures of oil, water and surfactant, in aqueous phase interact. The involvement of lignin based compound especially Lignosulfonate as non- petroleum chemical in EOR was started when the process of releasing trapped oil in abandoned oil field was assisted by using aqueous solution containing wood sulfite liquor(De & Bernhard, 1941). Lignosulfonate was used as an alternative to the more conventional petroleum sulfonate (Neale, Hornof, & Chiwetelu, 1981) and also served as a sacrificial agent in micellar flood by reducing the loss of primary surfactant through adsorption (Kalfoglou, 1977). Lignosulfonate was able to enhance the performance of primary surfactant in the surfactant formulation by reducing the interfacial tension and thus increased the oil recovery in oil displacement test (Neale et al., 1981). Selection of Lignosulfonate and other chemicals for the surfactant formulation were made by measuring the IFT using typical IFT measuring instrument. In this study, the lignin was extracted from both oil palm and local coconut coir then characterized using Fourier transform, infrared spectroscopy (FTIR) to compare the extracted lignin with the standard one, latter the extracted lignin was mixed with amine and sodium Dodecyl sulfate (SDS) to produce surfactant that were latter experimented on remobilizing residual oil after water flooding.
2. Methodology
2.1. Raw Material and Preparation
Two samples, coconut fiber and oil palm were selected as the raw materials coconut fiber raw material used in this study was obtained from local plantation while the oil palm raw material was supplied by a local company. In general this study was initiated by the soda pulping process to extract lignin from both oil palm and coconut fiber but before the pulping process they were soaked in water for cleaning then air dried to remove any contaminants. In general, figure 1 below shows the flow cycle of the experiment.
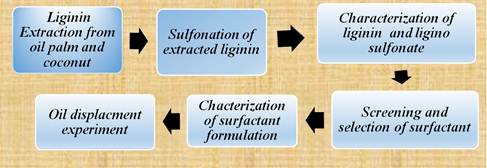
Figure 1. Flow cycle of the experiment.
2.2. Extraction of Lignin from the Raw Materials
The procedure of lignin extraction was done following the method used by (Ibrahim, Ibrahim, Azian, & Azian, 2005). In this method, the sample was cooked with sodium hydroxide in rotary digester for 3 hours at 170°C. Then cleaned, washed and dried, their moisture content analyzed using moisture analyzer to determine the amount of raw material needed in each soda pulping process using the equation below (Jaafar, Kamal, A Manan, Idris, & Junin, 2010)
(1)
Where,
gw = Actual (weighted) amount of raw materials(g)
ge = Theoretical (estimated) amount of raw material (g)
m = Moisture content of the sample
During the pulping process, Sodium hydroxide (NaOH) (99%purity, MW of 40.00g/mol) was used, to prepare the white liquor of lignin extraction process and the amount needed was 25% of the weight of the sample. The water used in each process was added depending on the weight of the sample and for appropriate formulations sample: water ratio of 1:8 was used. These materials (oil palm, coconut fiber, NaOH and water) were mixed in the 20 L stainless steel rotary digester. The process was accomplished after 3 hours at temperature of 170°C. Then, black liquor was separated from the pulp produced by squeezing and filtration. This filtration process was conducted using vacuum filtration through filter paper to remove all the small size fiber and any insoluble material for the better purity of lignin product obtained.
2.3. Sulfonation of Extracted Lignin
The sulfonation process was conducted following the procedure explained by (Adler & Karl, 1954), the previous extracted lignin powder was mixed with sulfonation agents which consisted of sodium sulfite, (Na2SO3) and de-ionized water in the glass bottle. The ratio of lignin to Na2SO3 to deionized water was fixed at 1:0.5:10. The pH of the mixture was initially 6.8 and in order to dissolve the lignin, 20% (w/v) NaOH solution was added and the resultant pH of the mixture added to 9. This mixture was then capped and heated until 80°C for 4 hours while stirring. After sulfonation, the mixture was then evaporated in the convection oven until a dried solid was obtained and crushed to fine powder using mortar and pestle. This fine powder Lignosulfonate then stored in bottle for subsequent process and analysis as shown in figure 2.
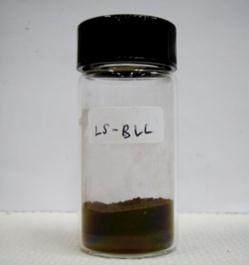
Figure 2. Lignosulfonate produced after sulfonation process.
2.4. Characterization of the Extracted Lignin
Perkin Elmer Spectrum One Fourier Transform Infra-Red (FTIR) spectrometer was used to characterize the extracted lignin compound from coconut fiber and oil palm EFB through the use of infra-red (IR) light. Each chemical substance absorbs IR energy differently. This test can detect even the smallest amounts of differences between the lignin from coconut fiber, oil palm and the standard lignin. The procedures of characterization using FTIR begun by mixing the dried extracted lignin with potassium bromide (KBr) and pressed into pellets under pressure to form a thin KBr discs. Then the absorption frequency spectra was recorded and plotted. The FTIR spectrometer provides the adsorption spectrum in percentage incident intensity, along the wave numbers 4000 to 400 cm-1. Besides, the IR spectrum of standard lignin was also run using the same method that further used to identify the functional group present in extracted lignin.
2.5. Surfactant Formulation Containing Lignin
The extracted lignin from the above experiments were almost identical to standard lignin based on the characterization using Fourier Transform Infra-Red (FTIR) and were now used in formulating the lignin based surfactant, this was done by mixing octadecylamine (0.15 g), extracted lignin (0.52 g) and sodium Dodecyl benzene sulfonate (SDBS) surfactant (0.7 g of 80% w/w) in a small mixing bottle. Brine (48.65 g of 10000 ppm) was added to this mixture. The bottle was capped and the contents were warmed and maintained at about 65oC in a water bath and stirred for approximately 5 hours. The resulting solution contained 0.3% by weight octadecylamine, 1.0% by weight lignin and 0.7% by weight SDBS. The blend was prepared at a level of 2% total active surfactant. After one day, the blend was examined for evidence of phase instability or precipitate formation. Eighty blends containing 0.1% to 0.5% (w/w) of octadecylamine, 0.1% to 1.8% (w/w) of SBDS surfactant and 0.1% to 1.8% (w/w) of extracted lignin were prepared in similar fashion. Then the whole procedure was repeated using the extracted oil palm and coconut fiber lignin (Kieke, 1999) and the final products were tested for their ability to remobilize oil after water flooding.
2.6. Oil Displacement Test
The effectiveness of the newly developed surfactant was tested through micro displacement using artificial porous medium. Figure 3 shows the schematic diagram of the oil displacement apparatus
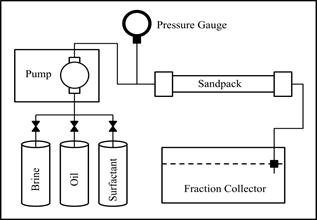
Figure 3. Experimental apparatus for oil displacement test.
Brine 10,000 ppm NaCl solution and industrial paraffin were used as the aqueous and oleicphasesinthe experiments respectively. The flooding was conducted at room temperature. Sand pack holder of 2.5 cm in diameter and length of 30 cm were used to represent the reservoir condition the porosity, permeability and pore volume were determined before the surfactant flooding. With the sand pack placed horizontally, brine was injected until it was 100% saturated. To represent the residual oil saturation, oil was injected until irreducible water saturation, Swir was reached and the Porous media was aged for 1 day and then flooded by the same brine until residual oil saturation, Sor was achieved. This was designed to represent the secondary recovery the oil remaining in the reservoir after water flooding was then subjected to injection of newly developed surfactant to remobilize more oil.
3. Results and Discussions
3.1. Soda Pulping Process of the Samples
Soda pulping was performed for degradation of lignin into smaller, water-soluble fragments and separates the aqueous black liquor from the fibrous carbohydrate materials. The coconut fiber and oil palm were cooked with 25%. Soda pulping and other type of alkaline pulping process were conducted at relatively high temperature. As the temperature increased, the reaction rates increased due to additional vibration energies applied to the bonds. Also, the hydroxide ion could act as a strong base at 170°C in water (Gierer, 1980)
3.2. Lignin Recovery from Black Liquor
Lignin was recovered from the black liquor through the acid precipitation process by converting soluble lignin into a solid form at pH below the pKa of phenolic group. In this study, sulfuric acid was selected rather than other mineral acid. By dissociating into two H+ and a SO42- ion in water, the usage of sulfuric acid produced a considerate amount of solid lignin at the end. Since the lignin recovered was to be sulfonated into Lignosulfonate, this selection of acid could reduce contamination of other types of ion in the solid lignin during sulfonation process. Black liquor initially had a pH of 13 and density of 1.05 g/ml. The pH was reduced by titrating sulfuric acid and lignin started to precipitate at pH around 5. Then, this titration was stopped when the solution reached pH2. During acid precipitation process, addition of sulfuric acid should how ever be controlled to avoid the formation of foam. Foam could easily form at pH around 5.0 to 7.0 and it was expected to be caused by the emission of gas when sulfuric acid reacted with some material in the black liquor. This foam can be very rigid and the sulfuric acid could not be titrated evenly. Lignin precipitates were recovered from the solution by vacuum filtration method. The precipitate were accumulated on the filter paper in the form of filter cake and washed several times with de-ionized water. The pH of this de-ionized water was adjusted using similar acid used for previous acid precipitation process. This step was done to remove excessive inorganic salts and organic contaminants for the better purity of lignin product.
3.3. Sulfonation of Lignin
Sulfonation of lignin was conducted to convert this water insoluble compound into brownish water-soluble Lignosulfonate (Figure 2). It was important to produce a water soluble product since typical surfactant slug of surfactant flooding are prepared and injected in the aqueous form. In the reaction mechanism, lignin initially converted into a quinone method. This intermediate formed by the loss of hydroxyl group at benzyl (α) carbon position of aromatic ring in the lignin structure. Then, sulfonate group acted as a nucleophile and introduced to the α-carbon position to form a Lignosulfonate.
3.4. FTIR Spectroscopy of Lignosulfonate
From the infrared spectroscopy, IR spectra of lignin obtained are shown in Figure 4 and 5 visually there was no difference between the spectrum of standard lignin and that extracted from oil palm and coconut fiber lignin. Pine wood based lignin was used as the standard lignin. The strong and broad band at 3412 cm-1 (standard lignin) and 3435 cm-1 (extracted oil palm lignin) indicate the characteristic of OH group or phenolic compound. The band at 1374 cm-1 (standard lignin) and 1375 cm-1 (extracted oil palm lignin) are due to the bending of vibration in phenolic OH group, while the band at 1042 cm-1 (standard lignin) and at1042 cm-1 (extracted oil palm lignin) are characteristic of primary alcohol.
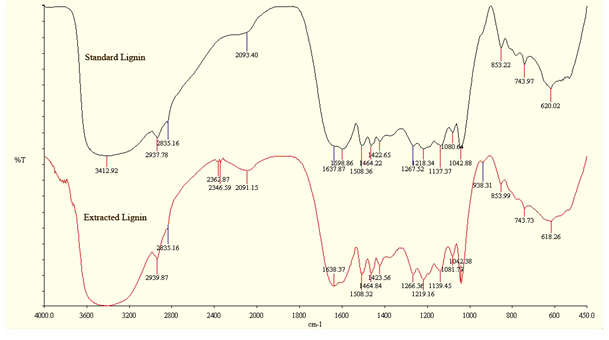
Figure 4(a). FTIR spectra of standard lignin and extracted oil palm lignin.
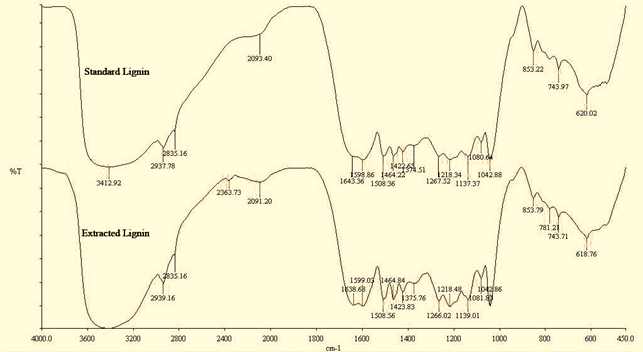
Figure 4(b). FTIR spectra of standard lignin and extracted coconut fiber.
Visually also based on the above Infrared spectrum in figure 4(b) for coco nut fiber derived lignin and standard lignin, almost there are no significant difference. From the above result, it shows that the extracted lignin contained hydroxyl (O-H) and carbonyl (C=O) functional group that can contribute to stable surfactant formulation
3.5. Interfacial Tension Measurement
Interfacial tension (IFT) measurement was done using IFT 700 tensiometer and Pendant drop method was used to measure the IFT of the surfactant formulation produced. The IFT of the formulation were measured at normal (room) condition and high pressure and temperature (HTHP) only. Stable formulations determined from stability test were measured to determine their IFT value. For IFT measurement at HTHP condition, pressure was set constantly at 1750 psi and temperature was set in the range between 50°C to 100°C. The IFT data between surfactant formulation and oil phase were obtained to evaluate the ability of the formulation to reduce IFT. For the surfactant effect, Figures 5 (a) and 5(b), when the amount of surfactant increased, the IFT value was decreasing. However, the slope was varied depending on the amount of amine used, as the amine used increased, the slope become steeper. Because some surfactant formulations reach the critical micelle concentration (CMC), as the concentration of SDBS increased, there was little change on the IFT value of the formulation. Further beyond the CMC, no change in IFT occurred. Surfactant added in excess of the CMC contributed to the formation of micelle and didn’t increase the concentration at the water/hydrocarbon interface. Thus, there is only a small incremental effect on IFT.
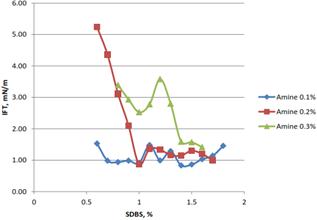
Figure 5(a). Effect of% of SDBS in the formulation on the IFT for coconut lignin.
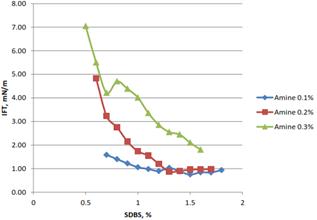
Figure 5(b). Effect of% of SDBS in the formulation on the IFT for oil palm lignin.
In IFT measurements, only selected formulation of lignin were used. The selection on the formulation was done based on the stability and the IFT value. The three stable formulations that produced lower IFT value were selected for both oil palm and coconut fiber. Table 1 show the selected formulation for IFT measurement.
Table 1. Selected formulation for IFT measurement.
Type of Lignin | Formulation | IFT Value (mN/m) |
| SDBS-C 4 | 0.86 |
Coconut Fiber | SDBS-C 5 | 0.83 |
| SDBS-C 9 | 0.91 |
| SDBS-E 2 | 0.84 |
Oil Palm EFB | SDBS-E 3 | 0.84 |
| SDBS-E 4 | 0.75 |
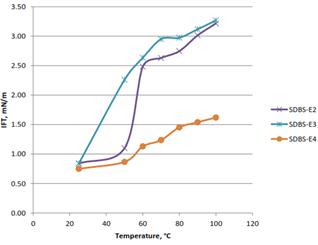
Figure 6(a). Effect of temperature on the IFT for oil palm lignin formulations.
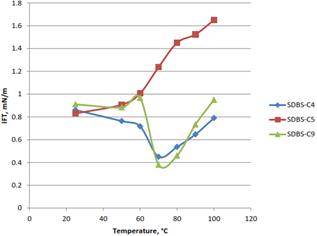
Figure 6(b). Effect of temperature on the IFT for coconut fiber lignin formulations.
Since temperature is one of the factors that affect the IFT, it is important to investigate the behavior of the formulation in high temperature condition which exists in the reservoir. Three formulations from each source (oil palm and coconut fiber) were used for this investigation. Figure 6(a), show that for oil palm formulations, increase in temperature caused the IFT to increase, increase in temperature caused solubilization parameters to decrease at optimal salinity, increasing IFT and shifting the optimal salinity for a given system to a higher value (Phan, Brown, White, Hodgson, & Jessop, 2009). However, the result for coconut lignin slightly varies as shown in Figure 6(b), only SDBS-C5 behaves like oil palm EFB lignin while SDBS-C4 and SDBS-C9 fluctuate as the temperature increase. At the range of 60°C to 80°C, the IFT for SDBS-C4 and SDBS-C9 was decrease to lower IFT before they rise at temperature range of 80°C to 100°C.
3.6. Oil Displacement
In the displacement test, seven set of experiments were carried out using six different samples of surfactant blends (SDBS-C4, SDBS-C5, SDBS-C9, SDBS-E2, SDBS-E3, SDBS-E4) and one using surfactant SDBS alone as a control experiment. The porosity, permeability, pore volume and initial water saturation of each were determined. All the experiments were carried out at ambient temperature. The oil displacement tests were carried out according to the scheme in Figure 7. The mentioned scheme can be divided into two major steps which begin with water flooding and followed by surfactant flooding.
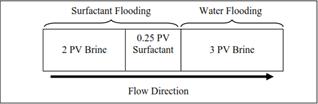
Figure 7. Displacement test slug size and sequence.
The average recovery from water flooding using all the formulations was almost the same before injecting the surfactant followed by the 3PV of brine behind the surfactant slug to act as a driving force for the surfactant slug to sweep through the beads packed model. The oil recovery by volume of surfactant injected was plotted in Figure 8. from the plot that sample containing formulation E4 (SDBS-E4) only yielded the highest recovery (15.18% of ROIP), followed by SDBS (11.98% of ROIP), formulation C5 (SDBS-C5, 11.38% of ROIP), formulation E3 (SDBS-E3,9.17% of ROIP), formulation E2 (SDBS-E2, 8.55% of ROIP), formulation C4 (SDBS-C4, 8.44% of ROIP), and formulation C9 (SDBS-C9, 6.87% of ROIP) at the end of the flood experiment.
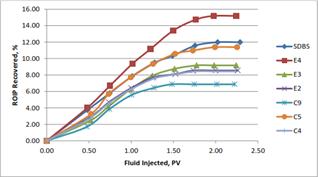
Figure 8. Correlation between percent of oil recovered and fluid injected after water flooding.
For evaluation of the additional recovery due to surfactant flooding, the percentage of original oil in place recovered was plotted in Figure 9 the highest recovery was obtained by formulation E4 (SDBS-E4), which has recovery of 4.10% of OOIP. The lowest recovery was from formulation C9 (SDBS-C9) which yielded 1.93% of OOIP. This was because formulation C9 (SDBS-C9), had the highest IFT (0.91 mN/m) and hence resulted into the lowest tertiary recovery. On the contrary, formulation E4 (SDBS-E4) which had the lowest IFT (0.75mN/m), resulted in highest tertiary recovery (4.10% of OOIP). Obviously the lower the IFT a surfactant had, the higher recovery of OOIP it could achieve. For formulation E2 (SDBS-E2) and E3 (SDBS-E3), the IFT value are same but have different recovery value. This happen due to dissimilarity of the pore orientation in both glass-beads packs that were used in this oil displacement process.
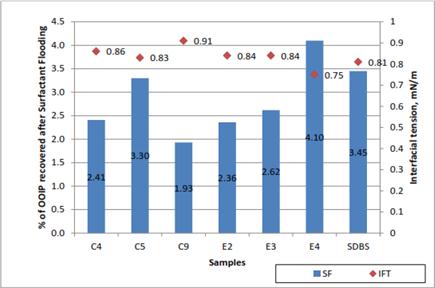
Figure 9. Correlation between residual oil recovered and IFT for each sample.
4. Conclusions
The formulations from oil palm lignin, SDBS-E4 formulation that consisted of 1.5% of Sodium Dodecyl Benzene Sulfate (SDBS), 0.4% of oil palm lignin and 0.1% octadecyl amine had the lowest interfacial tension (IFT) of 0.75mN/m and were stable after 24 hours. For formulations from coconut fiber lignin, SDBS-C5formulationthat consisted of 1.4% of Sodium Dodecyl Benzene Sulfate (SDBS), 0.5% of coconut fiber lignin and 0.1% octadecyl amine had the lowest interfacial tension (IFT) of 0.83 mN/m and was stable after 24 hours. Although coconut fiber gave higher yield of lignin compare to oil palm, formulation produced from oil palm performed better compared to those from coconut fiber lignin and for oil displacement the formulations from oil palm lignin, SDBS-E4 formulation gave the highest recovery of 4.10% of oil originally in place (OOIP) after surfactant flooding while formulations from coconut fiber lignin, SDBS-C5 formulation gave the highest recovery of 3.30% of oil originally in place (OOIP) after surfactant flooding. Comparing to SDBS which recover 3.45% of oil originally in place (OOIP), SDBS-E4 perform better in the oil displacement while SDBS-C5 gave lower recovery than SDBS.
Acknowledgment
The authors are grateful to university of Teknologi Malaysia and the Ministry of science, Technology and Innovations for awarding the research grant.
References
- Adler, Erich, & Karl, Mauritz Hagglund Erik. (1954). Method of producing water-soluble products from black liquor lignin: Google Patents.
- Bera, Achinta, Ojha, Keka, Mandal, Ajay, & Kumar, T. (2011). Interfacial tension and phase behavior of surfactant-brine–oil system. Colloids and Surfaces A: Physicochemical and Engineering Aspects, 383(1), 114-119.
- Dawe, Richard A. (1991). Enhancing oil recovery. Journal of Chemical Technology and Biotechnology, 51(3), 361-393.
- De, Groote Melvin, & Bernhard, Keiser. (1941). Flooding process for recovering oil from subterranean oil-bearing strata: Google Patents.
- Donaldson, Erle C, Chilingarian, George V, & Yen, Teh Fu. (1989). Enhanced oil recovery, II: Processes and operations: Elsevier.
- Gierer, Josef. (1980). Chemical aspects of kraft pulping. Wood Science and Technology, 14(4), 241-266.
- Ibrahim, MN Mohamad, Ibrahim, MN Mohamad, Azian, H, & Azian, H. (2005). Extracting soda lignin from the black liquor of oil palm empty fruit bunch. Jurnal Teknologi (C), 42(C), 11-20.
- Jaafar, Wan, Kamal, Wan Mohammad, A Manan, Muhammad, Idris, Ahmad Kamal, & Junin, Radzuan. (2010). Application of lignin from oil palm empty fruit bunch (EFB) in surfactant formulation. Journal of Materials Science and Engineering, 4(7), 55-61.
- Kalfoglou, George. (1977). Lignosulfonates as sacrificial agents in oil recovery processes: Google Patents.
- Kieke, Dan Edward. (1999). Use of unmodified kraft lignin, an amine and a water-soluble sulfonate composition in enhanced oil recovery: Google Patents.
- Lake, Larry W, & Venuto, Paul B. (1990). A niche for enhanced oil recovery in the 1990s. Oil & Gas Journal, 88(17), 62-67.
- Morrow, Norman R, & Mason, Geoffrey. (2001). Recovery of oil by spontaneous imbibition. Current Opinion in Colloid & Interface Science, 6(4), 321-337.
- Neale, Graham, Hornof, Vladimir, & Chiwetelu, Christopher. (1981). Importance of lignosulfonates in petroleum recovery operations. Canadian Journal of Chemistry, 59(13), 1938-1943.
- Phan, Lam, Brown, Heather, White, James, Hodgson, Allan, & Jessop, Philip G. (2009). Soybean oil extraction and separation using switchable or expanded solvents. Green chemistry, 11(1), 53-59.
- Reed, Ronald L, & Healy, Robert N. (1977). Some physicochemical aspects of microemulsion flooding: a review. Improved Oil Recovery by Surfactant and Polymer Flooding, 383-437.
- Schramm, Laurier L, & Marangoni, D Gerrard. (2000). Surfactants and their solutions: basic principles: Cambridge University Press: Cambridge, UK.
- Wang, Demin. (2002). Method for enhancing oil recovery efficiently is initiated by injecting into a subterranean oil-bearing formation, an aqueous polymer solution as a preceding-slug. y periodically injecting simultaneously or alternately a non-condensible gas: Google Patents.